Introduction
Aviation safety statistics are crucial for understanding the risks associated with flying. They provide insights that help improve safety protocols and design more resilient aircraft. Among various factors impacting aviation safety, corrosion stands out as a significant culprit. Corrosion can silently compromise aircraft integrity, leading to incidents that might otherwise be preventable.
Corrosion isn’t just an engineering issue; it’s a safety hazard. It’s like that pesky rust on your bicycle—if ignored, it can lead to catastrophic failure. In aviation, this translates to serious accidents, potentially endangering lives. By analyzing corrosion-related incidents, we can uncover patterns that help enhance maintenance practices and regulatory measures.
This article will cover essential themes regarding aviation accidents and incidents attributed to corrosion. First, we’ll define key terms associated with aviation accidents and incidents. Next, we’ll dissect the critical role of corrosion in aviation safety, including its types and effects on aircraft components. Finally, we’ll provide statistical insights and case studies that illustrate the real-world implications of corrosion in aviation.
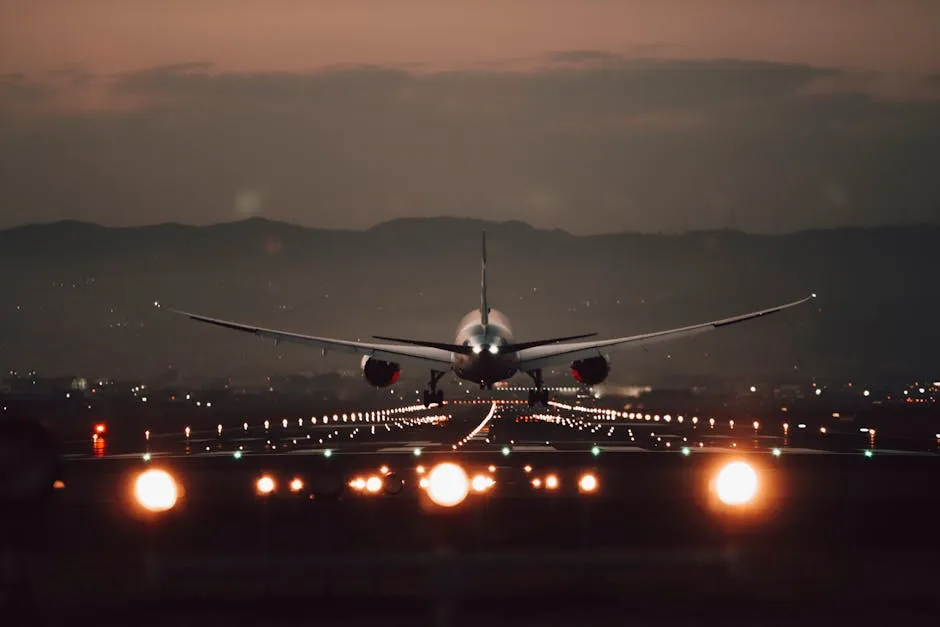
Understanding Aviation Accidents and Incidents
Definition of Key Terms
Accident: According to ICAO standards, an accident involves an occurrence linked to aircraft operation that results in serious injury or fatalities, or significant damage to the aircraft.
Incident: An incident is any occurrence that affects or could affect the safety of operations but does not meet the criteria for an accident. Both accidents and incidents are vital for understanding aviation safety.
Importance of Statistics
Tracking aviation accident rates is vital for several reasons. First, it informs safety improvements, as patterns in accident data can reveal underlying issues. For example, if corrosion is frequently noted in reports, it signals a need for enhanced maintenance protocols.
Secondly, these statistics drive regulatory changes. Regulatory bodies rely on data to create rules that protect passengers. When trends indicate a rise in corrosion-related incidents, regulators can mandate stricter inspections and maintenance practices.
In summary, aviation safety statistics are not mere numbers. They are the lifeline of an industry striving for continuous improvement and risk reduction. By understanding and addressing corrosion’s impact on aviation safety, we can ensure more secure skies for everyone.
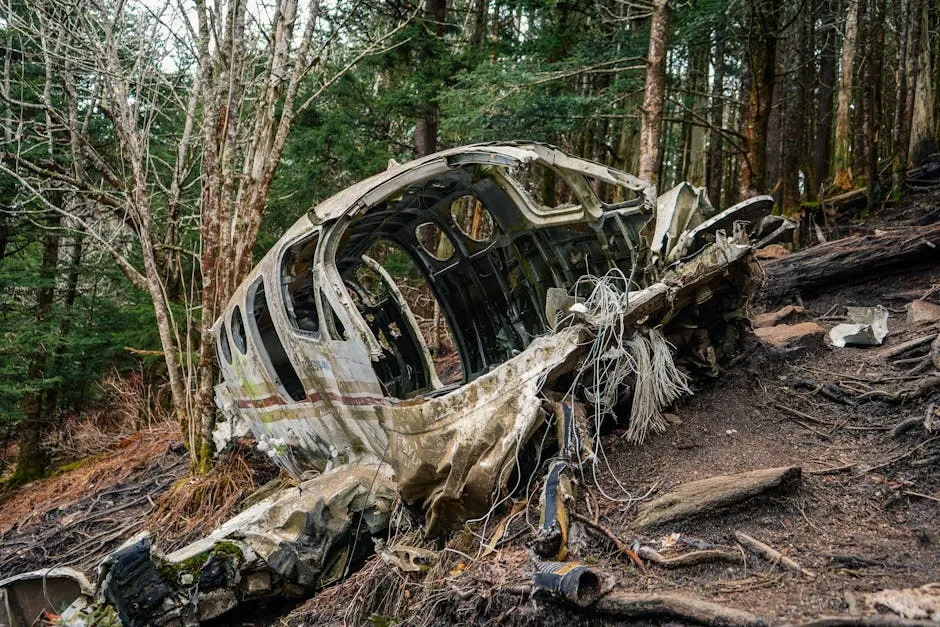
The Role of Corrosion in Aviation Safety
What is Corrosion?
Corrosion is a natural process that deteriorates materials, particularly metals. In aviation, it manifests in several forms, including pitting and stress corrosion cracking. Pitting occurs when localized areas of corrosion penetrate the metal surface, while stress corrosion cracking can lead to sudden structural failures.
Impact of Corrosion on Aircraft Components
Corrosion primarily affects critical aircraft components such as the fuselage and engine parts. The consequences can be dire; undetected corrosion can lead to system failures, which may result in accidents. Regular inspections are essential to catch these issues early and prevent catastrophic failures.
By understanding corrosion’s role in aviation safety, we can implement preventive measures. This includes employing advanced materials resistant to corrosion and enhancing maintenance practices. It’s not just about keeping planes flying; it’s about ensuring they do so safely and reliably.
In the next section, we will delve into the statistical overview of aviation accidents related to corrosion, exploring historical trends and current data. This will help us frame the conversation around maintaining safety standards in aviation.

For those interested in diving deeper into aviation safety, consider checking out some Aviation Safety Books. They can provide you with comprehensive insights into the protocols and technologies aimed at keeping aircraft safe.
Statistical Overview of Aviation Accidents Related to Corrosion
Historical Trends in Aviation Accidents
Aviation accidents have seen significant fluctuations over the decades. From the early days of flight to the present, the data reveals a pattern that reflects improvements in technology and safety protocols. According to the National Transportation Safety Board (NTSB), the number of aviation accidents peaked in the 1990s, with approximately 9.08 accidents per 100,000 flight hours. Fortunately, these figures have steadily declined, hitting 0.80 accidents per million sectors in 2023.
However, corrosion as a factor in these accidents warrants attention. Historical data indicates that corrosion-related failures have contributed to a portion of the accidents. A notable example is the Embraer EMB-120RT accident in 1995, where a fatigue crack from corrosion led to a propeller blade failure, resulting in seven fatalities. This case illustrates how unnoticed corrosion can evolve into a life-threatening situation.
Graphs illustrating the trends of aviation accidents over the years reveal that while overall accident rates are declining, the impact of maintenance-related issues, including corrosion, has been increasingly recognized. Maintenance-related accidents accounted for about 2.0% of all accidents between 1941 and 1997, rising to approximately 3.8% from 1998 to 2019. This trend highlights the escalating importance of rigorous maintenance processes to combat corrosion.

Current Statistics
As of 2023, current statistics present a stark picture of aviation safety. The aviation industry recorded 30 accidents, with one fatal incident resulting in 72 fatalities. While these figures are encouraging, the correlation between corrosion and incidents remains a significant concern. Recent studies indicate that human error accounts for about 80% of aviation accidents, with mechanical failure trailing behind.
Corrosion-related incidents stand out when compared to other causes. Data from various reports indicate that corrosion contributes to a notable percentage of mechanical failures. For instance, the NTSB identified that nearly 36% of maintenance-related accidents stem from system component failures, many of which can be traced back to corrosion issues.
The aviation sector must maintain a keen focus on corrosion-related statistics. With the increase in aircraft age and operational hours, the likelihood of corrosion-related incidents may rise without proper maintenance. Current regulations emphasize the importance of routine inspections to identify and mitigate corrosion before it leads to serious accidents. It’s clear that while overall aviation safety is improving, the fight against corrosion remains an ongoing battle that must be addressed to ensure the future safety of air travel.
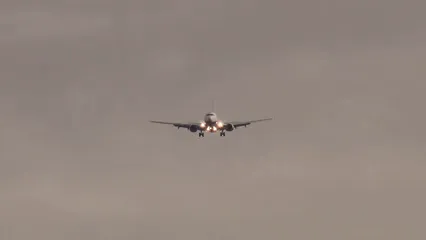
Case Studies of Corrosion-Related Accidents
Notable Accidents
Case Study 1: Embraer EMB-120RT Accident Overview
On August 21, 1995, tragedy struck with the Embraer EMB-120RT (Flight 529) near West Georgia Regional Airport. This aircraft, operated by Atlantic Southeast Airlines, was en route from Atlanta to Gulfport. Approximately 30 minutes into the flight, disaster loomed. At an altitude of 18,100 feet, a propeller blade from the left engine snapped, resulting in a catastrophic loss of control. The crew declared an emergency, but despite their efforts, the aircraft crashed, claiming the lives of seven passengers and the captain.
The National Transportation Safety Board (NTSB) investigation revealed a startling truth: the blade fracture stemmed from a fatigue crack linked to multiple corrosion pits. These pits went undetected due to inadequate maintenance procedures, illustrating how corrosion can lurk unnoticed, waiting for the right moment to strike.
Case Study 2: Boeing 737-300 Incident
Another significant incident occurred with a Boeing 737-300 during a flight from Los Angeles to Seattle. The aircraft experienced a sudden cabin depressurization, forcing an emergency descent. Investigation revealed that corrosion had compromised the integrity of a critical fuselage component, leading to structural failure. Although the flight landed safely, the incident raised alarms about the consequences of neglecting corrosion inspections. Understanding how corrosion can lead to sudden, life-threatening failures is essential for maintaining aviation safety.

Lessons Learned
Both incidents shed light on the critical importance of rigorous maintenance practices. The NTSB findings from the EMB-120RT accident emphasized the need for comprehensive inspections and regular checks for corrosion. Maintenance procedures must evolve to include advanced detection methods. Corrosion can silently wreak havoc, making it imperative for airlines to prioritize corrosion management.
These accidents catalyzed regulatory changes, leading to stricter guidelines for propeller inspections and airframe maintenance. As a result, the aviation industry has implemented enhanced training programs focused on corrosion awareness, ensuring that maintenance personnel understand the signs and risks associated with corrosion.
By learning from these tragic events, the aviation sector aims to foster a culture of proactive maintenance. Emphasizing the significance of corrosion detection can prevent future incidents, safeguarding the lives of passengers and crew alike.
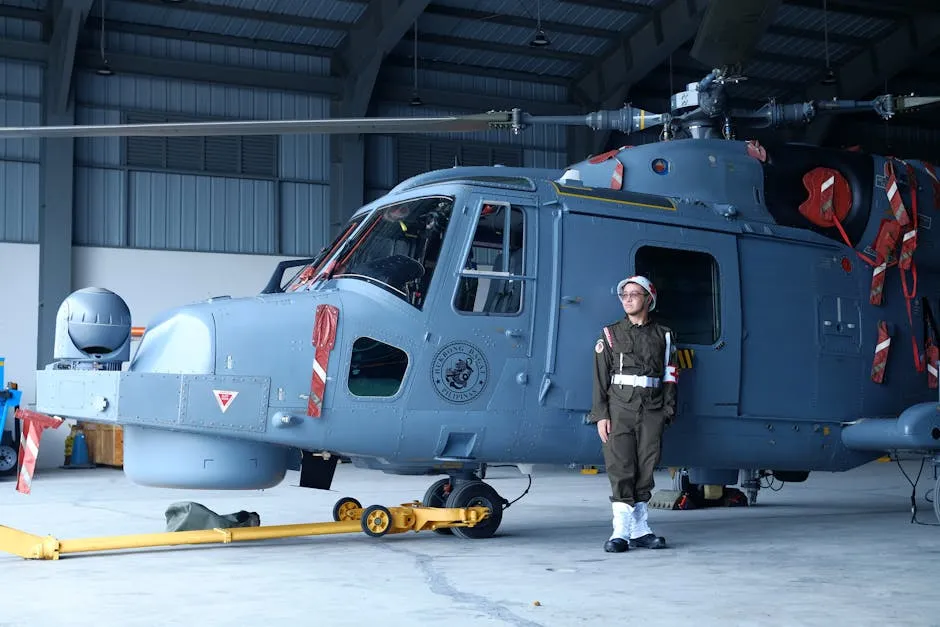
Maintenance Practices and Corrosion Prevention
Importance of Regular Maintenance
Regular maintenance is the backbone of aircraft safety and a crucial strategy for preventing corrosion-related incidents. Without a robust maintenance routine, corrosion can thrive, leading to potentially catastrophic failures. Think of maintenance as a regular health check-up for your aircraft—skip it, and you might find yourself facing some serious issues down the line.
Standard maintenance practices include thorough inspections, cleaning, and the application of protective coatings. These elements are vital in identifying early signs of corrosion. Inspections should focus on areas prone to corrosion, such as joints, fasteners, and engines. Neglecting these checks can lead to system failures and, in the worst-case scenario, accidents.
Additionally, the industry has introduced advanced technologies to combat corrosion. For example, ultrasonic testing can detect subsurface corrosion that isn’t visible to the naked eye. This proactive approach not only enhances safety but also extends the lifespan of aircraft components. If you’re looking for quality Ultrasonic Testing Equipment, now is the time to invest!
Furthermore, airlines are encouraged to adopt a culture of continuous improvement when it comes to maintenance practices. By investing in training for maintenance personnel, airlines ensure that their teams are equipped with the latest knowledge and techniques for corrosion prevention. Regular workshops and training sessions can empower staff to recognize corrosion risks and address them promptly.
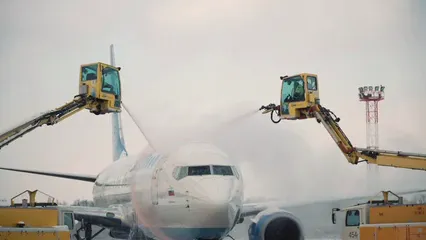
In summary, regular maintenance is non-negotiable for aviation safety. By prioritizing corrosion prevention, the industry can significantly reduce the risk of corrosion-related incidents, ensuring that every flight is as safe as possible.
Innovations in Corrosion Prevention
Corrosion is the silent enemy of aviation. To combat this, new technologies and materials are emerging. One exciting innovation is the use of advanced coatings. These coatings create a barrier against moisture and corrosive agents. Think of them as sunscreen for aircraft! For those interested in protective measures, check out these Protective Coatings for Metals.
Another notable advancement is the introduction of lightweight composite materials. These materials are less susceptible to corrosion compared to traditional metals. Not only do they reduce weight, but they also enhance fuel efficiency. It’s like getting a gym membership for your aircraft—who doesn’t want to shed a few pounds?
Additionally, researchers are exploring smart sensors that can detect early signs of corrosion. These sensors provide real-time data, allowing maintenance teams to address issues before they escalate. Imagine having a corrosion whisperer on your team, always alerting you to potential problems!
Regular inspections are still crucial, but with these innovations, the aviation industry is taking significant strides in corrosion prevention. As technology continues to evolve, the fight against corrosion becomes more effective, ensuring safer skies for all.
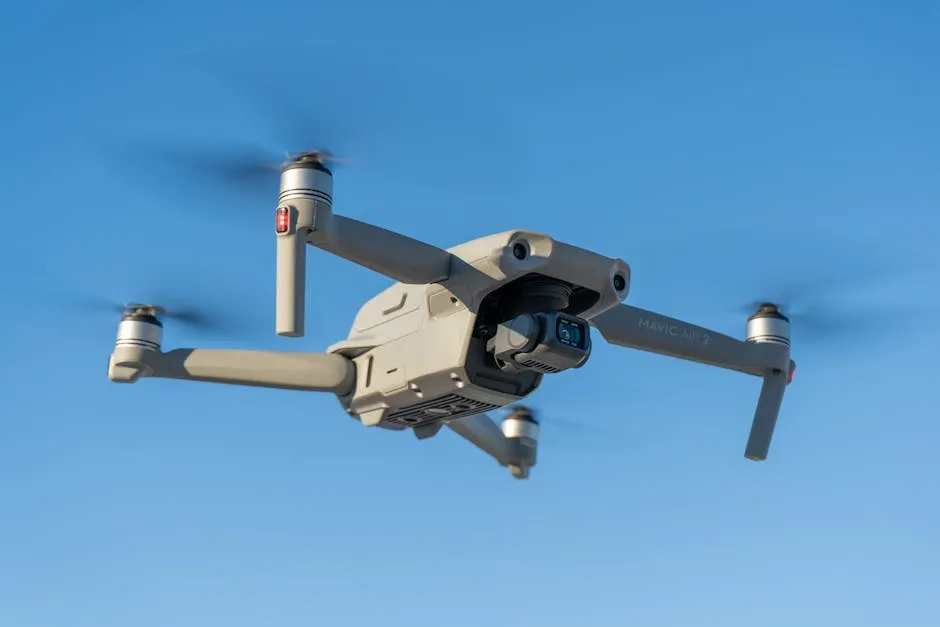
Regulatory Measures and Industry Standards
Overview of Aviation Regulations
Aviation is a highly regulated industry, with safety at its core. Key regulatory bodies like the FAA (Federal Aviation Administration) and EASA (European Union Aviation Safety Agency) establish strict guidelines for aircraft maintenance and safety. Their regulations cover everything from inspection protocols to maintenance procedures, ensuring that aircraft remain airworthy throughout their operational life.
The FAA mandates that operators conduct regular maintenance checks based on flight hours and calendar time. This includes routine inspections, which are critical in identifying potential issues like corrosion. Similarly, EASA has its own set of maintenance regulations that align closely with international safety standards. These regulations are designed to protect passengers and crew by ensuring aircraft are maintained to the highest safety standards.
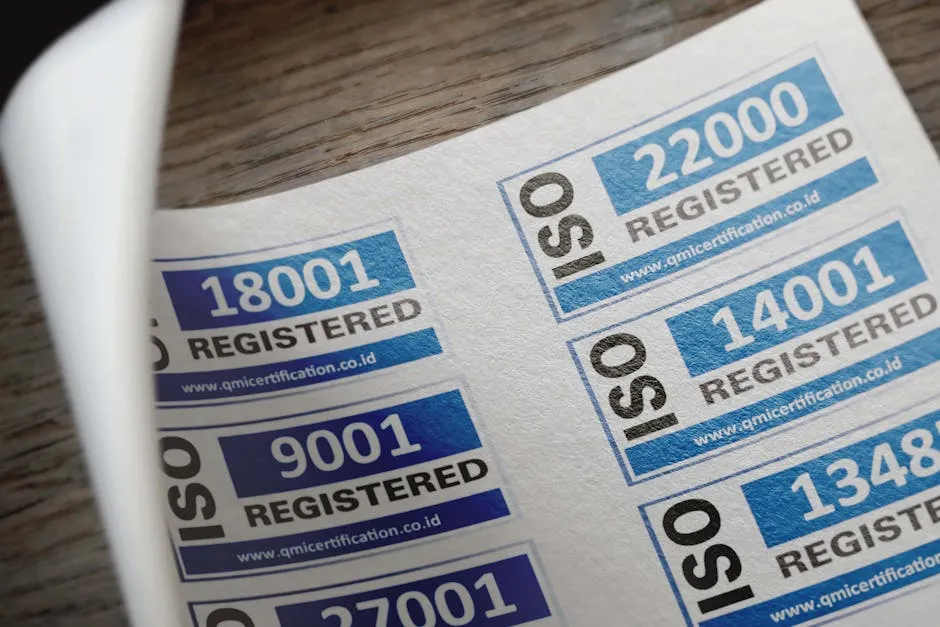
Corrosion-Specific Regulations
Corrosion poses a unique threat to aviation safety, prompting regulators to implement specific measures. The FAA has published Advisory Circulars that provide guidelines on corrosion prevention and control. These documents detail best practices for inspecting and maintaining critical components vulnerable to corrosion, such as fuselages and engine parts.
Moreover, the industry has developed corrosion management programs tailored for different aircraft types. These programs emphasize the importance of preventive maintenance and regular inspections. Manufacturers like Boeing and Airbus also provide maintenance manuals that include corrosion inspection criteria specific to their aircraft.
Additionally, the NTSB (National Transportation Safety Board) often highlights corrosion-related findings in its investigations. This can lead to recommendations for regulatory updates or additional training for maintenance personnel. By fostering a culture of awareness and adherence to these regulations, the aviation industry aims to reduce the risks associated with corrosion.
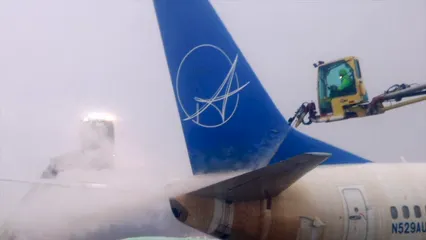
Conclusion
Understanding corrosion’s impact on aviation safety is crucial. It can silently lead to catastrophic failures if left unchecked. The statistics reveal a clear link between corrosion and incidents, making it imperative to address this issue proactively.
Ongoing research and innovation are vital for developing new materials and technologies that resist corrosion. These advancements, combined with strict adherence to maintenance protocols, can significantly reduce corrosion-related incidents. The aviation industry must prioritize these efforts to ensure safer skies for everyone.
As we move forward, collaboration between regulatory bodies, manufacturers, and airlines will be essential. Together, they can create an environment where safety is paramount, and the threat of corrosion is minimized. By investing in research and embracing new technologies, we can continue to enhance aviation safety and protect the lives of passengers and crew.
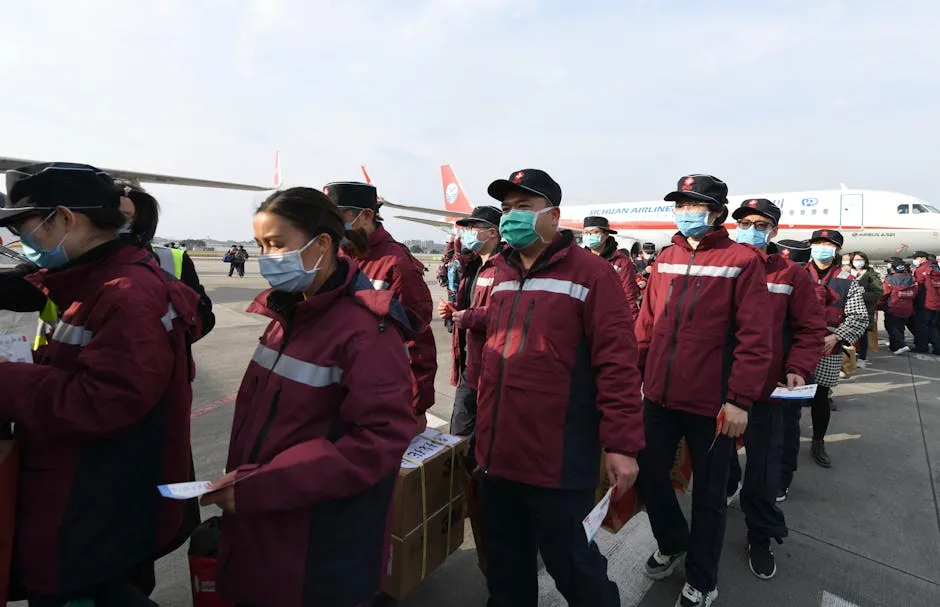
FAQs
What are the most common causes of aviation accidents?
Aviation accidents can be attributed to various factors. Statistics reveal that human error is responsible for about 80% of these incidents. This includes mistakes made by pilots and air traffic controllers, especially during critical phases like takeoff and landing. Mechanical failures follow closely, accounting for around 21% of accidents. Within this category, corrosion plays a significant role. In fact, nearly 36% of maintenance-related accidents stem from system component failures, many of which can be traced back to corrosion in aircraft parts. As aircraft age, the risk of corrosion increases, making vigilant inspection and maintenance crucial for safety.
How can corrosion be prevented in aircraft?
Preventing corrosion is a top priority for aircraft maintenance. Regular inspections are essential to catch early signs of corrosion. Maintenance practices include cleaning surfaces, applying protective coatings, and ensuring proper drainage. Using advanced materials that resist corrosion can also be effective. Aircraft manufacturers are increasingly utilizing lightweight composites that offer better resistance. Furthermore, training maintenance personnel to recognize corrosion risks enhances overall safety. A culture of proactive maintenance can significantly reduce corrosion-related incidents, ensuring aircraft remain safe and airworthy.
What should I do if I suspect corrosion on my aircraft?
If you suspect corrosion on your aircraft, take immediate action. Report your concerns to your maintenance team or a certified technician. Provide as much detail as possible about where you noticed the issue. It is crucial to follow up with a thorough inspection. Technicians should conduct detailed examinations using appropriate methods, such as ultrasonic testing, to assess the extent of corrosion. If found, repairs should be made promptly to restore the aircraft’s integrity. Remember, addressing corrosion early can prevent severe consequences and enhance overall aviation safety.
Please let us know what you think about our content by leaving a comment down below!
Thank you for reading till here 🙂
For a deeper understanding of the statistics surrounding aviation accidents and incidents related to corrosion, consider reviewing our analysis on statistics of aviation accident and incident rate by corrosion.
And if you’re interested in enhancing your flying experience, don’t forget to check out some Aviation Headsets. They can make your flights a lot more enjoyable!
All images from Pexels