Introduction
Statistical Process Control (SPC) is a vital component in modern manufacturing and quality assurance. At its core, SPC employs statistical methods to monitor and control processes, ensuring that they operate efficiently while producing high-quality products. This approach not only minimizes waste but also enhances consistency, making it an indispensable tool for manufacturers aiming for excellence.
The roots of SPC trace back to the early 1920s when Walter A. Shewhart, a statistician at Bell Laboratories, introduced control charts. These charts were revolutionary, providing a visual means to track process stability. W. Edwards Deming later popularized these techniques, especially during World War II, when they were essential in improving production quality in military applications. Thanks to their pioneering efforts, SPC gained traction and has become standard practice across various industries.
This article aims to offer a comprehensive guide to implementing an SPC program. We will explore the tools involved, best practices for success, and the positive impact SPC can have on production processes. By the end of this post, you’ll have a solid understanding of how to leverage SPC to enhance quality and efficiency in your operations.
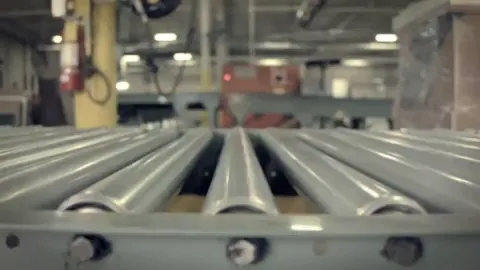
Understanding Statistical Process Control (SPC)
What is SPC?
Statistical Process Control (SPC) is a methodology designed to monitor and control manufacturing processes. By collecting and analyzing data in real-time, SPC helps organizations identify variations and take corrective actions before defects occur. This proactive approach shifts the focus from post-production inspection to continuous monitoring, allowing for immediate interventions when issues arise.
The methodology behind SPC revolves around the concept of process variation. Every manufacturing process experiences some level of variability, which can stem from common causes—normal fluctuations inherent to the process—or special causes, which are unexpected and often indicate a problem. By distinguishing between these two types of variation, SPC enables organizations to implement effective control measures.
The importance of measuring and controlling process variations cannot be overstated. By doing so, manufacturers can ensure products conform to specifications, reduce waste, and ultimately improve customer satisfaction. SPC is applicable in numerous sectors, from automotive to healthcare, proving its versatility and effectiveness in maintaining quality standards.
In summary, Statistical Process Control is not just a tool; it’s a philosophy that fosters a culture of continuous improvement. By embracing SPC, organizations can enhance their operational efficiency, reduce costs, and ultimately deliver better products to their customers.

The Benefits of Implementing an SPC Program
Quality Improvement
One of the most significant benefits of an SPC program is its ability to enhance product quality. By monitoring processes in real-time, SPC helps identify variations that could lead to defects. This proactive approach allows organizations to address issues before they escalate into major problems.
For example, a study showed that a manufacturer implemented SPC and saw a 40% reduction in defects within six months. Imagine that! A sudden drop in quality issues means happier customers and fewer returns. Another case involved a food processing plant that adopted SPC methods and achieved a 30% increase in product consistency. Quality improvement isn’t just a goal; it’s a tangible outcome of actively managing processes.
SPC also provides insights into process capability. By analyzing data, manufacturers can determine if their processes are performing within acceptable limits. This information is crucial for ensuring that products meet specifications consistently. Higher quality products lead to increased customer satisfaction and loyalty, which is a win-win for any business.
Looking to dive deeper into quality improvement? Consider grabbing a copy of the Statistical Process Control Book. It’s a great resource for anyone serious about elevating their quality management game!
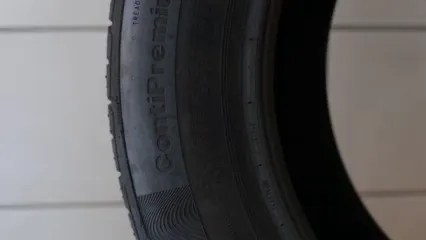
Cost Reduction
Cost savings are another compelling reason to implement an SPC program. By focusing on quality control, organizations can minimize waste and reduce scrap rates. Imagine a factory that previously tossed out 20% of its output due to quality issues. After adopting SPC, they managed to cut that scrap rate in half. That’s a significant cost reduction!
Additionally, SPC enables manufacturers to optimize their processes. By identifying inefficiencies, organizations can streamline operations, leading to lower production costs. Companies that have embraced SPC often report savings in the thousands—if not millions—of dollars annually due to these efficiencies.
Moreover, reducing waste translates to a lower environmental impact. Companies can take pride in knowing they are not only cutting costs but also contributing to sustainability efforts. Who knew that quality control could have such a positive effect on the bottom line and the planet?
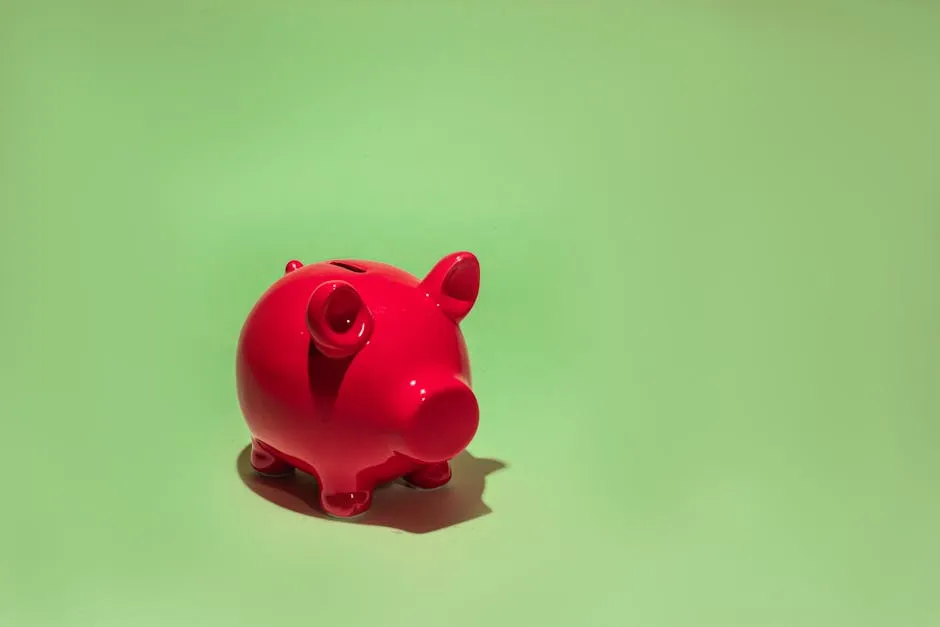
Enhanced Decision-Making
Data-driven insights from SPC empower better decision-making across the board. Real-time data collection and analysis allow managers to make informed choices quickly. No more relying on gut feelings or outdated information!
When employees have access to accurate data, they can identify trends and respond to issues faster. For instance, if a production line starts to show signs of variation, the team can investigate immediately instead of waiting for a monthly report. This agility can lead to quicker resolutions and less downtime, ultimately improving efficiency.
SPC also promotes a culture of accountability. With clear data on performance, everyone—from floor workers to management—understands their role in maintaining quality. This shared responsibility fosters teamwork and encourages everyone to strive for continuous improvement.
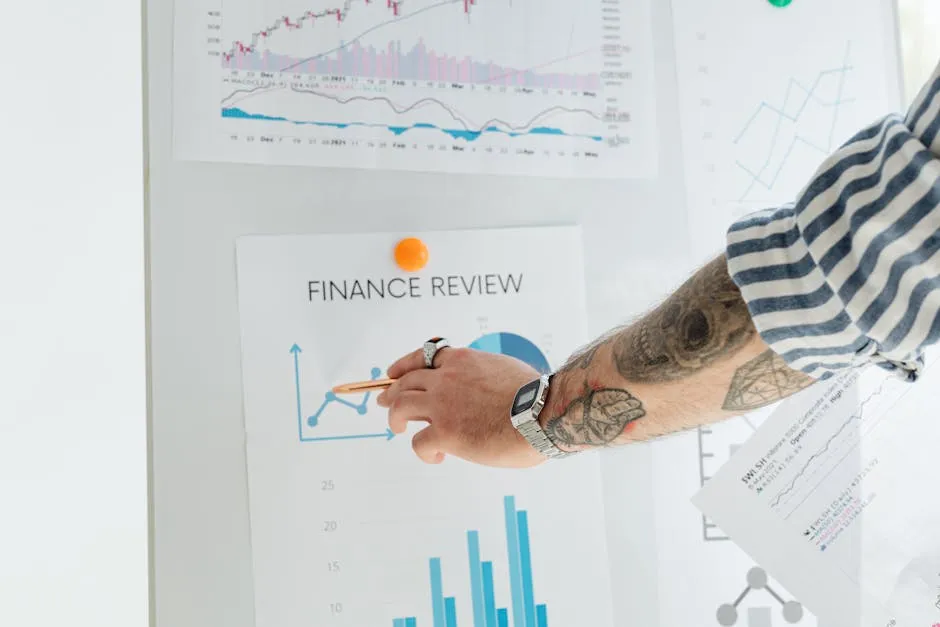
Continuous Improvement Culture
Implementing an SPC program isn’t just about monitoring processes; it’s about fostering a culture of continuous improvement. Organizations that embrace SPC often find that it encourages employees to seek out inefficiencies and propose solutions actively.
In a company where SPC is practiced, employees are more likely to feel empowered to voice their ideas. They know that their input can lead to real changes in the production process. This environment nurtures innovation and creativity, which are crucial for long-term success.
Moreover, SPC provides a structured approach to problem-solving. When issues arise, teams can utilize SPC tools to analyze data, identify root causes, and implement corrective actions systematically. This methodical approach reduces the likelihood of recurring problems, creating a more stable and efficient operation.
Looking for tools to help foster this culture? A Quality Control Tools Kit can be a game-changer for your team, providing everything needed to tackle quality issues head-on!

In essence, an SPC program lays the groundwork for ongoing improvement. By instilling a mindset of quality and efficiency, organizations can adapt and thrive in an ever-changing marketplace.
Steps to Implementing a Statistical Process Control Program
Step 1: Assessing Current Processes and Needs
Before jumping into the world of Statistical Process Control (SPC), it’s crucial to take a step back and assess where you currently stand. Think of this step as giving your processes a good ol’ health check. Start by gathering a cross-functional team. This team should include representatives from production, quality assurance, and operations. They will help you get a well-rounded view of the current processes.
Begin by mapping out your existing workflows. Document every step involved in your production process. This will help you visualize the areas where SPC can make a difference. Don’t be shy—ask questions! What processes are causing delays? Where do defects typically occur? This analysis will uncover the weak links in your production chain.
Next, collect data on current performance metrics. Look for trends over time. Are there specific times when defects spike? Are certain products more prone to quality issues? This data will guide you in pinpointing areas that need immediate attention. It’s like shining a flashlight in a dark room—you’ll see the corners that need cleaning!
Finally, prioritize the areas that require SPC the most. Focus on processes that have a direct impact on quality and customer satisfaction. Remember, the goal here is to identify specific processes where implementing SPC will yield the greatest benefits. With your analysis complete, you’re well on your way to a robust SPC program.
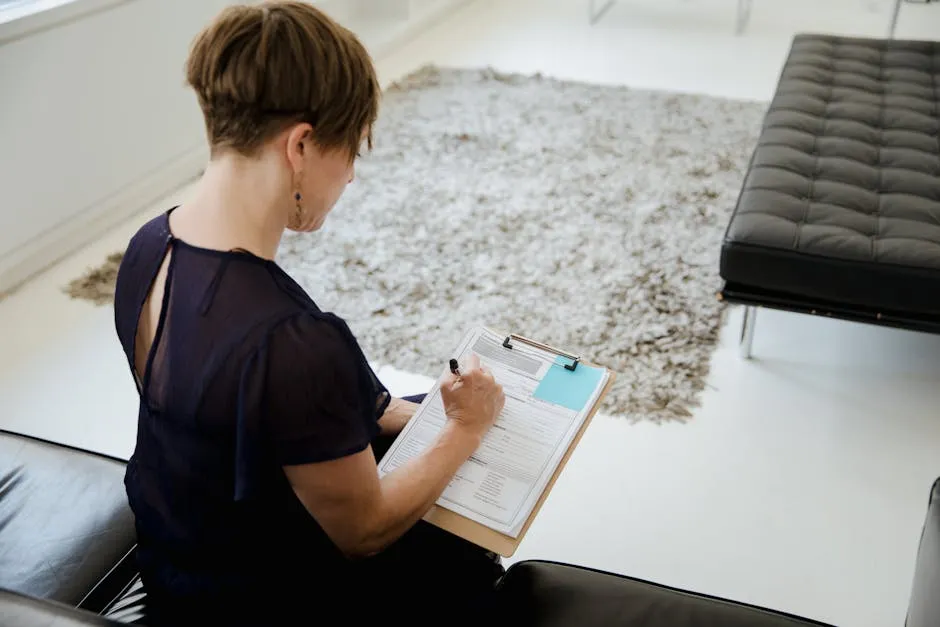
Step 2: Setting Clear Objectives
Now that you know where you stand, it’s time to set some clear objectives. Think of this step as creating a roadmap for your SPC journey. What do you want to achieve? Defining specific, measurable goals is key.
Start by aligning your objectives with your overall business goals. Do you want to reduce defects by a certain percentage? Or maybe you’re aiming to decrease production costs? Whatever it is, make sure it’s quantifiable. For instance, instead of saying “improve quality,” aim for “reduce defects by 20% within six months.”
Involve your cross-functional team in this process. Gather insights from different departments to ensure your objectives are realistic and achievable. This collaboration will foster a sense of ownership and commitment to the goals set.
Also, consider setting short-term and long-term objectives. Short-term goals create quick wins, while long-term goals keep everyone focused on the bigger picture. Remember, clear objectives will not only guide your SPC implementation but also help maintain motivation throughout the process.

Step 3: Selecting the Right Tools and Software
With your objectives in place, you’re ready to choose the right tools and software for your SPC program. This step is like picking the right ingredients for a delicious recipe. The right tools will help you collect, analyze, and interpret data effectively.
Start by evaluating the various SPC software options available. Look for features that cater to your specific needs. Real-time data collection is crucial. The ability to gather data on-the-fly will allow you to respond quickly to any deviations. You want software that can generate control charts effortlessly too. These charts visualize process performance, making it easier to spot trends and variations.
Consider looking into platforms like Minitab Statistical Software, ICONICS, or Siemens’ Opcenter Quality. Each offers unique features that might align with your processes. Check out user reviews and case studies to see how other companies have benefited from these tools.
Don’t forget about integration! Ensure that the software can seamlessly connect with your existing systems. Whether it’s your ERP system or quality management tools, smooth integration will save you time and headaches down the line.
Finally, prioritize user-friendliness. Your team should be able to navigate the software without feeling overwhelmed. After all, the goal is to enhance productivity, not create another obstacle!
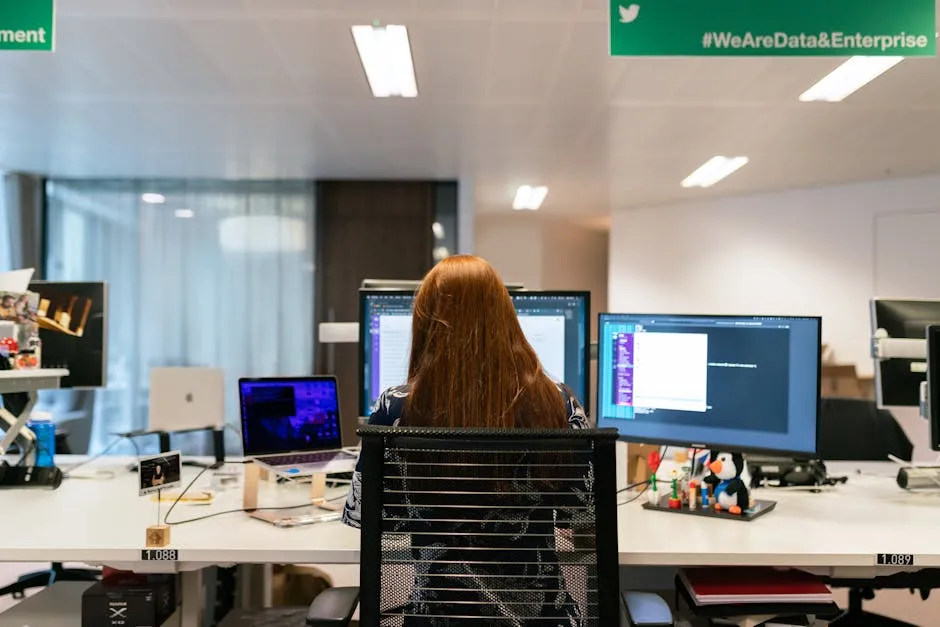
Step 4: Training and Involving Employees
You’ve done the groundwork, and now it’s time to involve the real heroes of your SPC program—your employees! Comprehensive training is essential for ensuring everyone is on board with the new processes and tools.
Start by designing a training program that covers the basics of SPC, its importance, and how it impacts their day-to-day tasks. Offer hands-on training sessions where employees can practice using the software and tools. This practical approach will help them feel more comfortable when it’s time to implement SPC in real scenarios.
Involve cross-functional teams in the training process too. Each department can offer unique insights and perspectives, making the sessions richer and more informative. Encourage employees to ask questions and share their experiences. This collaboration fosters a sense of community and collective responsibility.
Additionally, create a feedback loop. Regularly check in with employees to understand their challenges and successes with the SPC program. This will help you make necessary adjustments and show your team that their input is valued.
Moreover, recognize and celebrate milestones achieved through SPC. This boosts morale and reinforces the importance of continuous improvement. When employees feel included and valued, they are more likely to embrace the changes and contribute positively to your SPC journey.

Step 5: Data Collection and Monitoring
When it comes to Statistical Process Control (SPC), effective data collection is paramount. You can’t fix what you don’t measure, right? So, let’s look at some handy methods for gathering data.
Check Sheets are your best pals in this quest. These simple forms allow you to record data as it happens. They’re fantastic for tracking defects, process variations, or even down-time in production. You can customize them to capture exactly what you need. If you’re looking for a good set of Check Sheets for Data Collection, they can help you get started on the right foot!
Next up, we have Control Charts. These visual tools are essential for monitoring process behavior over time. They help distinguish between common cause variations—think of them as background noise—and special cause variations, which are the red flags that require immediate attention.
Now, how do you keep an eye on everything? Regular monitoring is key! Set up a schedule for reviewing the data. This could be daily, weekly, or whatever fits your operation. The goal is to catch those pesky variations before they escalate into larger issues.
When monitoring, be prepared to adapt. If you notice a trend indicating a deviation, it’s time to act! Whether it’s tweaking a machine or retraining staff, quick responses can save you a lot of hassle. Remember, the sooner you react, the less damage control you’ll need later!
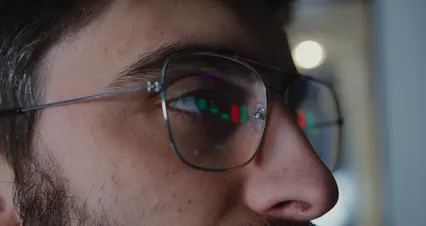
Step 6: Analyzing Data and Making Adjustments
Once you’ve collected the data, it’s time to roll up your sleeves and analyze it. How do you spot trends or variations? Start by plotting the data on your control charts. Look for patterns. Are there points that seem to dance outside the control limits? Those are your special causes, and they need attention.
Another helpful technique is Pareto Analysis. This method helps you identify the most common types of defects. You can then focus on addressing those issues that have the most significant impact. Think of it as the 80/20 rule—fixing 20% of the problems can lead to 80% of the improvements.
But analysis isn’t just about spotting problems; it’s also about taking corrective actions. If you identify a trend indicating a shift in process performance, act quickly! Maybe it requires a machine calibration or a process tweak.
Also, make sure to communicate findings with your team. Sharing data insights fosters a collaborative environment and encourages everyone to contribute to the improvements. This teamwork can lead to innovative solutions that you might not have considered alone.
In summary, data analysis is crucial in SPC. It reveals insights that drive decision-making and adjustments. Remember, in the world of manufacturing, standing still is not an option. Continuous improvement is the name of the game!
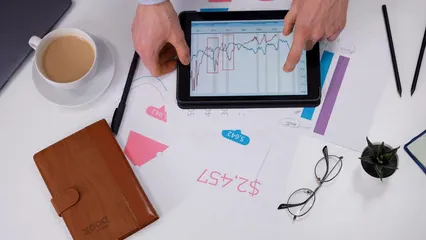
Key Tools Used in SPC
Control Charts
Control charts are the backbone of any Statistical Process Control program. They’re graphical tools used to track process variations over time. But what do they really do? Well, they help you determine whether a process is in control or if it’s throwing a tantrum.
There are several types of control charts. The X-bar chart monitors the average of a process over time, while the R-chart focuses on the range of variation within a set of samples. Each type serves a specific purpose, so it’s essential to choose the right one for your needs.
For instance, if you’re dealing with a manufacturing process where measurements fluctuate, the X-bar chart will help you keep tabs on those averages. Meanwhile, the R-chart will flag any unusual spikes in variation that could signal a problem.
But that’s not all! Control charts provide visual cues that help operators quickly identify when processes are veering off course. By analyzing the data plotted on these charts, you can pinpoint when and why variations occur. This allows for timely interventions, ultimately improving product quality and consistency.

Flowcharts and Process Mapping
Flowcharts are another essential tool in your SPC toolkit. They help visualize processes, making it easier to identify areas needing improvement. Picture this: a detailed flowchart of your production line can highlight bottlenecks or redundancies that may not be obvious at first glance.
Using symbols and arrows, flowcharts map out each step in a process. This can reveal inefficiencies or steps that don’t add value. By simplifying complex processes, flowcharts empower teams to streamline operations effectively.
Moreover, involving your team in creating flowcharts can lead to valuable insights. Employees who work on the floor often have the best understanding of the process. Their input can pinpoint areas for improvement that might not be apparent through data alone.
Incorporating flowcharts into your SPC program creates a visual roadmap for continuous improvement. So, don’t underestimate their power! They’ll not only enhance understanding but also foster a culture of collaboration and innovation.
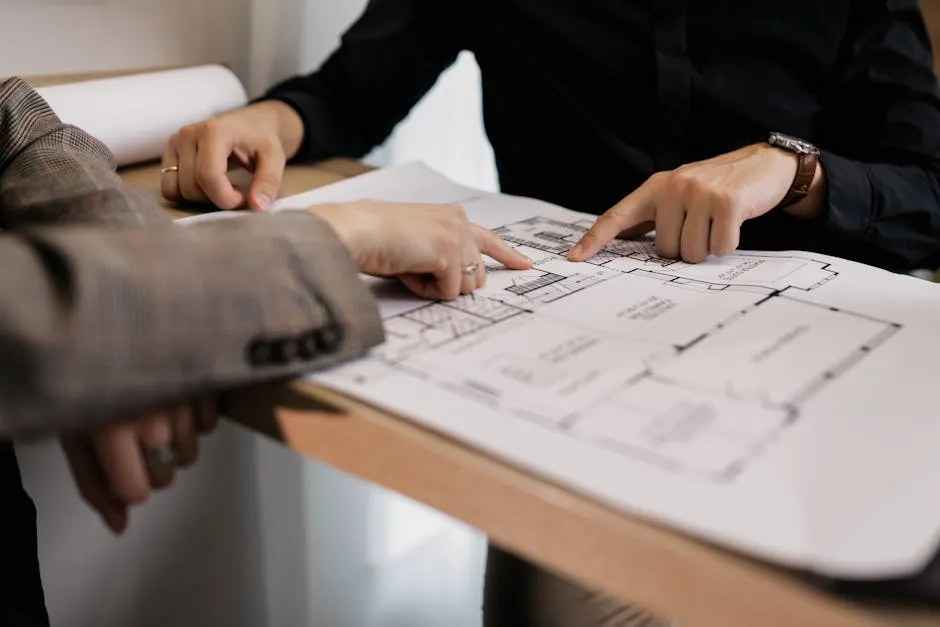
Cause-and-Effect Diagrams
Cause-and-effect diagrams, often referred to as fishbone diagrams, are vital tools in identifying potential causes of quality issues. Picture this: you’re at a dinner party, and the host asks why the soup tastes a bit off. Instead of pointing fingers, you brainstorm various ingredients and processes that could lead to this flavor fiasco. That’s precisely what these diagrams do for your production processes!
By visually mapping out various potential causes, teams can systematically investigate and pinpoint root issues, whether they stem from materials, methods, or machinery. This approach not only helps in identifying problems but also fosters collaboration and communication among team members. When everyone contributes to the discussions, it creates a shared understanding of quality challenges, making it easier to address them effectively.
In the manufacturing realm, utilizing cause-and-effect diagrams allows teams to break down complex problems into manageable parts. They can categorize causes into groups, such as man, machine, method, material, and environment. This organized approach can reveal surprising insights—like how a minor machine malfunction could lead to significant quality deviations.
Ultimately, these diagrams are more than just a troubleshooting tool; they embody a proactive stance toward quality management. By identifying potential causes early, teams can implement solutions before issues escalate into costly defects.

Check Sheets and Histograms
Check sheets and histograms are the unsung heroes of data collection and analysis in SPC. A check sheet is like a simple checklist, but it’s oh-so-much more. It’s a structured form that allows teams to capture real-time data effortlessly. Whether you’re counting defects, measuring process variations, or tracking occurrences, check sheets provide a straightforward way to gather valuable information.
Think of a busy pizza parlor where staff track customer orders. Using a check sheet, they can note each topping requested, making it easier to analyze popular choices later. Similarly, in manufacturing, these sheets help visualize patterns and trends in data, making it easier to spot anomalies or recurring issues.
On the flip side, histograms bring those check sheets to life! By converting raw data into graphical representations, histograms illustrate frequency distributions. They allow teams to visualize how often certain outcomes occur, revealing the underlying distribution of process data. This visual representation is crucial in identifying whether processes are stable or if there are signs of special cause variations.
For example, if a histogram shows that most products fall within acceptable weight limits but a few outliers exist, it’s a signal to investigate. By combining check sheets and histograms, organizations enable themselves to make data-driven decisions, ensuring that processes remain within control limits and quality standards are consistently met.
Challenges in Implementing an SPC Program
Resistance to Change
Implementing a Statistical Process Control (SPC) program often faces resistance from employees. Change can be daunting, and many workers might feel their daily routines are threatened. “Why fix what isn’t broken?” they may ask. This mindset can hinder progress and create friction within teams.
To overcome this resistance, effective communication is key. Clearly explain the benefits of SPC—like improved quality and reduced waste. Share success stories from other organizations to illustrate the positive impact of SPC. Show employees that this isn’t just another management fad; it’s a strategy that empowers them and enhances their work.
Involve employees early in the process. Create opportunities for them to voice concerns and provide input on how SPC can fit into their routines. When team members feel included, they are more likely to embrace change. Additionally, consider offering training sessions that equip employees with the skills they need to adapt. A well-informed team is a confident team!
Data Overload
In today’s data-driven world, the risk of overwhelming employees with information is real. When implementing an SPC program, organizations often gather vast amounts of data. Without a clear strategy, this data can quickly turn into noise rather than useful insights.
To manage this potential data overload, focus on relevant metrics. Identify key performance indicators (KPIs) that align with your objectives. Rather than drowning in data, teams should prioritize tracking what truly matters.
Utilizing data visualization tools can also help. Graphs, dashboards, and control charts can transform raw data into digestible insights. This makes it easier for employees to identify trends and variations without feeling lost in a sea of numbers.
Finally, establish a regular review process. Schedule routine meetings to discuss data findings, allowing teams to share insights and collaboratively address issues. By creating a structured approach to data analysis, organizations can harness the power of information while preventing overwhelm.
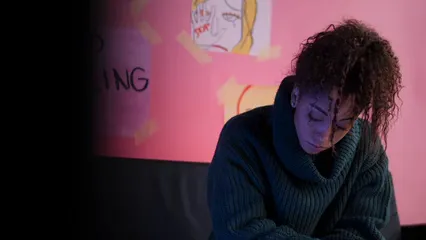
Maintaining Momentum
Sustaining enthusiasm for an SPC program over time can be challenging. Initial excitement may fade as the novelty wears off, and employees might slip back into old habits. So, how can organizations maintain momentum?
First, celebrate wins—big and small! Recognizing achievements boosts morale and reinforces the value of the SPC program. Whether it’s reducing defects or improving efficiency, share these milestones with the entire team.
Second, keep the lines of communication open. Regularly update employees on the program’s progress and solicit feedback. This not only keeps everyone informed but also shows that their input is valued. Engaged employees are more likely to stay committed.
Additionally, provide ongoing training and resources. As processes evolve, so should employees’ knowledge. Consider refresher courses or workshops to keep skills sharp and maintain interest.
Lastly, create a culture of continuous improvement. Encourage employees to take ownership of the SPC program, allowing them to identify areas for enhancement. When everyone feels invested in the process, motivation naturally follows.
Case Studies: Successful SPC Implementations
One of the best ways to understand the impact of Statistical Process Control (SPC) is through real-world examples. Let’s take a look at a few companies that successfully implemented SPC programs, highlighting their challenges and the lessons learned.
Case Study 1: Automotive Manufacturer
An automotive manufacturer faced rising defect rates in its assembly line. By implementing an SPC program, the company utilized control charts and cause-and-effect diagrams to identify issues. Within six months, defect rates dropped by 30%. The key takeaway? Engaging employees at all levels was essential. They not only provided valuable insights but also fostered a sense of ownership in the quality improvement process.
Case Study 2: Food Processing Plant
In a food processing plant, inconsistent product quality was leading to customer complaints. The company adopted SPC tools, including check sheets and histograms, to monitor key quality metrics. After a year, they achieved a 25% increase in product consistency. A critical lesson learned was the importance of continuous monitoring. Regularly reviewing data helped the team catch deviations before they escalated into larger issues.
Case Study 3: Electronics Manufacturer
An electronics manufacturer struggled with high scrap rates due to process variability. By implementing SPC, they focused on real-time data collection and analysis. This led to a 40% reduction in scrap over the course of a year. The company learned that investing in robust training for employees was crucial to the program’s success, ensuring that everyone understood how to use the tools effectively.
Conclusion
Statistical Process Control (SPC) is an essential tool for modern manufacturing. By implementing an SPC program, companies can enhance product quality, reduce costs, and foster a culture of continuous improvement. The benefits are clear: improved efficiency, reduced waste, and increased customer satisfaction.
As you consider implementing an SPC program in your operations, remember that the journey may present challenges. However, the long-term benefits of investing in quality control and continuous improvement far outweigh the initial hurdles. Embrace the process, engage your team, and watch as your organization transforms into a more efficient, quality-driven powerhouse.
In summary, SPC is not just a methodology; it’s a mindset that prioritizes quality and efficiency. By adopting this approach, businesses can stay competitive in an ever-evolving marketplace, ultimately leading to greater success and sustainability.
FAQs
What industries benefit from SPC?
SPC is widely applicable across various sectors, including manufacturing, healthcare, and service industries. Any process where output can be measured for conformity to specifications can benefit from SPC.
How long does it take to implement an SPC program?
Implementation timelines can vary based on the organization’s size and complexity. Generally, it can take anywhere from a few months to over a year to fully integrate SPC into existing processes.
What is the cost of implementing SPC?
Costs may include software purchases, training expenses, and potential consulting fees. However, the long-term savings from reduced waste and increased efficiency often outweigh these initial investments.
How do I choose the right SPC software?
Evaluate your organization’s specific needs, including features like real-time data collection, user-friendliness, and integration capabilities with existing systems. It’s crucial to involve end-users in the selection process to ensure the software meets their needs.
Can SPC be used in non-manufacturing processes?
Absolutely! SPC can be applied to repetitive processes beyond traditional manufacturing, such as financial auditing, healthcare, and IT operations. Its versatility makes it a valuable tool across various industries.
Please let us know what you think about our content by leaving a comment down below!
Thank you for reading till here 🙂
All images from Pexels