Introduction
Imagine a world where your production line runs smoother than a well-oiled machine. Enter Statistical Process Control (SPC), a superhero for productivity and quality! SPC is all about using statistical methods to monitor and control processes. It ensures that you’re not just throwing spaghetti at the wall to see what sticks—nope, we’re talking about data-driven decisions!
At the heart of SPC are charts that help visualize data over time, known as SPC charts. These nifty little tools are significant in quality control because they reveal trends, patterns, and anomalies. They help you identify when processes are running smoothly and when they need a little TLC.
But why should you care about SPC charts? Well, they come with a treasure trove of benefits! Industries ranging from manufacturing to healthcare have embraced them. SPC charts lead to less waste, improved efficiency, and a happier customer base. As your business aims to enhance quality and efficiency, this article will guide you through the essentials of SPC charts, their components, and how to implement them effectively. Buckle up; it’s time to transform your processes!

Understanding Statistical Process Control (SPC)
What is Statistical Process Control?
Statistical Process Control (SPC) is a quality management methodology that uses statistical methods to monitor and control a process. The main goal is to ensure that the process operates efficiently, producing products that meet quality standards consistently.
The roots of SPC trace back to the 1920s when Dr. Walter Shewhart introduced the concept at Bell Laboratories. He aimed to provide a systematic approach for identifying and reducing variations in processes. Over the years, SPC has evolved, further popularized by experts like Dr. W. Edwards Deming, particularly after World War II when it was adopted widely in manufacturing.
SPC focuses on two types of variations: common cause and special cause. Common cause variation is the background noise, the everyday fluctuations that happen in any process. On the other hand, special cause variation is the unexpected spike in performance, often due to specific, identifiable factors. Understanding these variations is crucial for effective quality management.
If you’re looking to dive deeper into the world of SPC, consider picking up SPC Charts: A Practical Guide to Statistical Process Control. This book can help you understand how to implement SPC effectively in your organization and avoid common pitfalls.
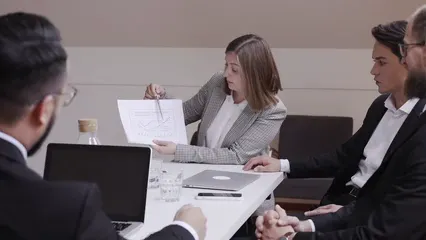
Importance of SPC in Quality Management
SPC is not just a fancy buzzword; it’s a powerful tool for monitoring processes and reducing variability. By employing SPC, businesses can identify when a process is going off track and take corrective actions before issues escalate.
Industries like manufacturing, healthcare, and service sectors reap significant benefits from SPC. For instance, in manufacturing, SPC helps maintain product consistency, reducing defects and rework. In healthcare, it can monitor patient outcomes over time, ensuring that care processes remain stable and effective.
In service industries, SPC can assist in tracking customer satisfaction trends, leading to proactive improvements. By leveraging SPC, organizations can not only enhance operational efficiency but also foster a culture of continuous improvement. So, whether you’re in a factory or a hospital, SPC can be your trusty sidekick in the quest for quality and efficiency.
To further enhance your understanding of quality management, check out Lean Six Sigma for Service: How to Use Lean Speed and Six Sigma Quality to Improve Services and Transactions. This book provides insights into how to improve service processes effectively.

Components of SPC Charts
Structure of SPC Charts
Statistical Process Control (SPC) charts are powerful tools in quality management. They help visualize process performance over time, making it easier to spot trends and variations. Three key components make up every SPC chart: the Central Line (CL), the Upper Control Limit (UCL), and the Lower Control Limit (LCL).
The Central Line (CL) represents the average or mean of the data collected. It serves as a baseline for comparison. If your data points hover around this line, congratulations! Your process is likely under control.
Next, we have the Upper Control Limit (UCL). This line sits above the Central Line and represents the maximum acceptable level of variation in your process. It’s calculated by taking the average and adding three times the standard deviation. Why three? Because this threshold captures about 99.7% of process data under normal conditions. If a data point strays above this limit, it’s a signal that something might be amiss.
Conversely, the Lower Control Limit (LCL) indicates the minimum acceptable variation. Like the UCL, it’s derived from the average, but here, you subtract three times the standard deviation. Any data point below this limit demands attention, as it suggests possible issues that could affect quality.
Calculating these limits is straightforward. First, gather a sample of your data. Then, compute the mean (average) and standard deviation. Use these values to establish your UCL and LCL. This simple formulaic approach ensures you’re equipped to maintain quality in your processes.

Types of Control Charts
SPC charts come in various flavors, each suited for different types of data and contexts. Here’s a quick overview of some popular types:
- X-bar and R Charts: Ideal for monitoring the mean and range of a process. Use these when you have subgroups of data.
- P Charts: Perfect for attribute data, these charts track the proportion of defective items in a sample.
- C Charts: Focused on the count of defects per unit, these charts work well when you want to monitor the number of nonconformities.
- U Charts: Similar to C Charts but used for varying sample sizes. They help track defects per unit in a sample.
- EWMA Charts: Exponentially Weighted Moving Average charts are effective for detecting small shifts in the process mean over time. They’re particularly useful when you want to monitor long-term trends.
Knowing when to use each type is crucial. For instance, if you’re dealing with a manufacturing process that produces items in batches, X-bar and R charts are your best friends. However, if you’re analyzing a service process where you track defects, P charts might be more appropriate.
In summary, understanding the components and types of SPC charts is fundamental for effective quality control. By leveraging these tools, you can identify trends, maintain process stability, and ensure your operations run smoothly. So, whether you’re monitoring a manufacturing line or tracking a service process, there’s an SPC chart that fits your needs.
If you’re looking for a comprehensive reference, check out The Lean Six Sigma Pocket Toolbook: A Quick Reference Guide to Nearly 100 Tools for Improving Quality and Speed. This guide is perfect for anyone looking to enhance their SPC knowledge with practical tools.

Common Mistakes in SPC Implementation
Implementing Statistical Process Control (SPC) can feel like walking a tightrope. One misstep, and your data could tumble into chaos. Common mistakes often occur during the setup and execution phases of SPC. Let’s highlight some of these pitfalls and how to sidestep them.
First, many organizations fail to collect quality data. Without accurate data, your SPC charts will be about as useful as a chocolate teapot. Proper data collection involves establishing clear measurement criteria. Always use consistent sampling methods. Random sampling can lead to skewed results, making it an unreliable foundation for analysis.
Another frequent error? Ignoring the importance of training. A well-prepared team can make or break your SPC success. Ensure that all team members understand not just how to use SPC charts, but why they matter. Training should cover the intricacies of data collection, chart maintenance, and interpretation.
Additionally, organizations often neglect documentation. Comprehensive records of data collection and chart analysis are critical. Without documentation, how will you trace back errors or variations? Skipping this step is like trying to solve a mystery without clues. Keep detailed logs of all data points, methods, and analyses to facilitate future investigations.
Lastly, one must emphasize the importance of control limits. Some teams mistakenly set arbitrary limits based on gut feelings rather than statistical calculations. Control limits should be derived from historical data and statistical formulas. If these limits are incorrectly established, your SPC charts will mislead rather than guide.
In summary, avoid these common mistakes by focusing on quality data collection, thorough training, diligent documentation, and accurate control limit calculations. Proper management of these aspects will lay a solid foundation for successful SPC implementation.
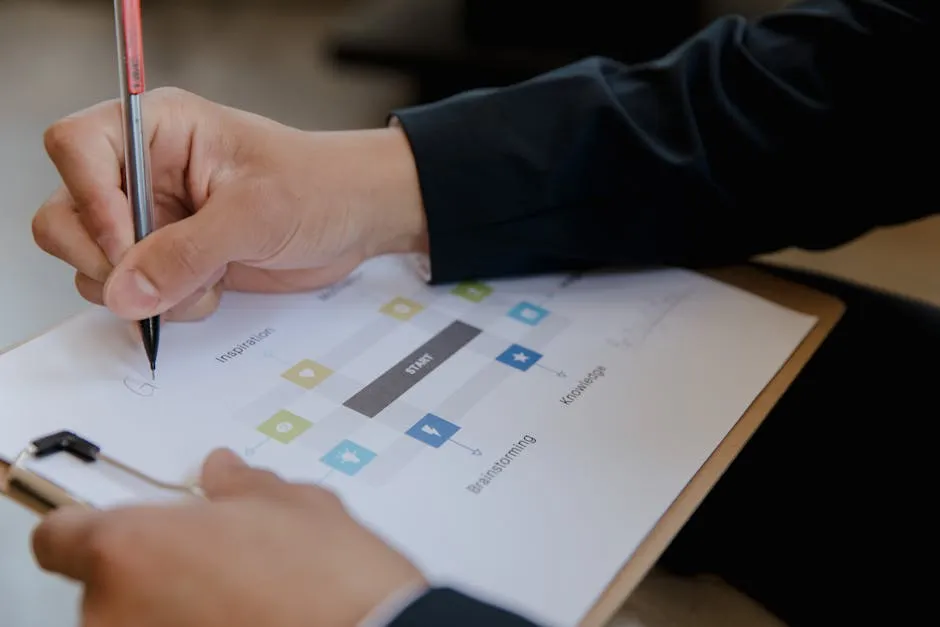
Analyzing SPC Charts
Identifying Special Causes of Variation
When analyzing SPC charts, it’s crucial to recognize when a process goes out of control. This recognition is the beacon guiding you toward necessary corrective actions. So, how do you determine if your process is in a state of chaos or calm?
Special cause variations usually signal that something unusual has happened in the process. Start by looking for data points that stray outside control limits. If a point pops up outside the Upper Control Limit (UCL) or dips below the Lower Control Limit (LCL), grab your detective hat—investigation time!
There are also rules to help identify these special causes. One rule states that if you have a single point beyond the control limits, it’s a red flag. Another rule suggests that if you see eight consecutive points all above or below the central line, you may be facing a trend.
Additionally, look for trends in the data. If you observe six consecutive points consistently increasing or decreasing, it’s not just a coincidence. This might indicate that your process has shifted, requiring your immediate attention. Remember, trends can be sneaky; they often creep up on you when you least expect it.
Lastly, keep an eye on the number of points close to the control limits. If two out of three points are near either limit, that’s also a sign to investigate further. These rules create a safety net, helping you catch issues before they escalate.

Interpreting Results
Once you’ve identified special causes, it’s time to interpret the results. Look closely at the trends in your data. Are there patterns emerging? These can reveal opportunities for process improvement, making analysis a treasure hunt.
Data documentation is your trusty sidekick here. Keep thorough notes on all changes, observations, and variations. When deviations occur, refer back to your documentation. It’s like having a map that leads you to the treasure—without it, you might find yourself lost.
Root cause analysis plays a vital role in this process. When you see a deviation, dig deep! Ask “why?” multiple times to uncover the underlying issues. This method of inquiry helps ensure you’re addressing the core problem rather than just putting a band-aid on the symptoms.
Finally, remember that interpreting SPC chart results isn’t about finger-pointing. It’s about collaboration and continuous improvement. Engage your team in discussions about findings. This approach fosters a culture of quality and shared responsibility.
By focusing on trends, maintaining thorough documentation, and conducting root cause analyses, you’ll be well-equipped to navigate the murky waters of process variation. Your SPC charts will transform from mere numbers into actionable insights that drive efficiency and quality improvements.
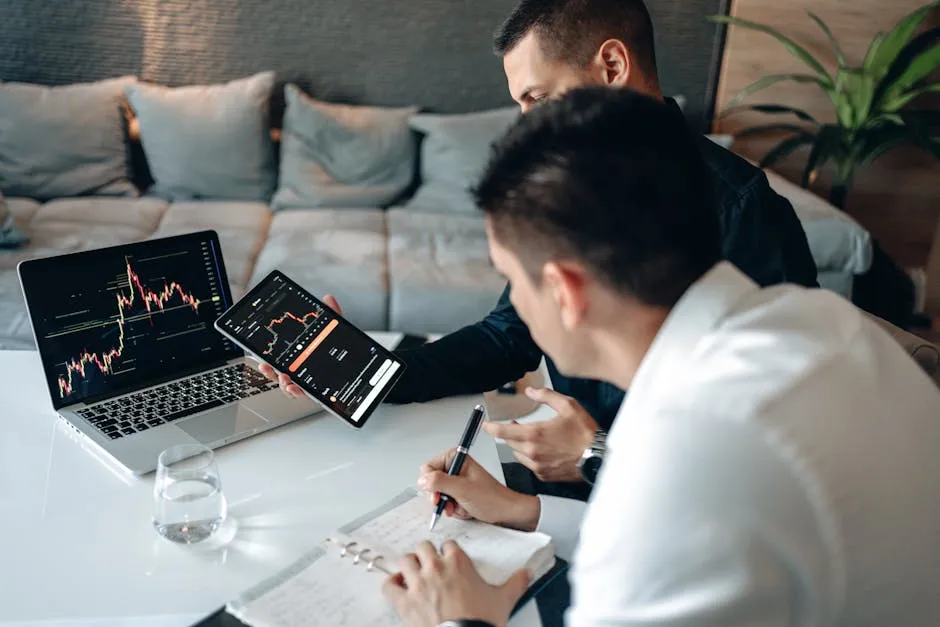
Benefits of Using SPC Charts
Advantages of SPC in Business Operations
SPC charts are like the Swiss Army knife of quality management—versatile and essential! They offer numerous benefits that can transform your business operations. Let’s break down some of the most significant advantages.
First, cost savings through waste reduction are hard to ignore. By monitoring processes with SPC charts, businesses can identify inefficiencies. This visibility enables corrective actions before issues escalate, leading to less waste and lower costs.
Additionally, SPC charts enhance process efficiency. By maintaining control over variations, you can optimize workflows. This efficiency not only boosts productivity but also ensures that resources are used more effectively.
Quality is another area where SPC shines. With consistent monitoring, you can identify defects early in the production process. This proactive approach ensures that products meet quality standards before they reach customers. In turn, this leads to increased customer satisfaction—happy customers mean repeat business!
Case studies abound that demonstrate successful SPC implementation. For instance, a manufacturing company reduced defects by 30% within six months of adopting SPC practices. Similarly, a healthcare provider used SPC to track patient wait times, resulting in a 20% improvement in service delivery. These real-world examples underscore the tangible benefits of SPC.
In summary, the advantages of SPC in business operations are clear. From cost savings and improved efficiency to enhanced quality and customer satisfaction, SPC charts are invaluable tools. Embrace them, and watch your business thrive!
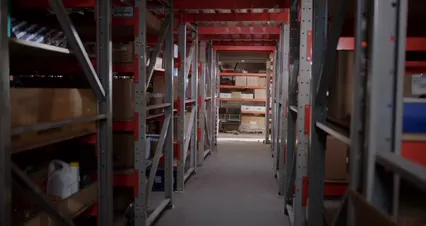
Continuous Improvement through SPC
Statistical Process Control (SPC) is the Swiss Army knife of quality management. It fits perfectly into broader continuous improvement initiatives like Lean and Six Sigma. These methodologies aim to enhance processes, reduce waste, and improve product quality—just like SPC does!
Lean focuses on eliminating waste and optimizing efficiency. Meanwhile, Six Sigma targets defects and process variations. SPC complements both by providing the tools to monitor and control processes effectively. Think of SPC as the trusty sidekick that helps you keep an eye on the process while you’re busy slashing waste and defects.
SPC charts make it easy to visualize process performance over time. They help organizations recognize trends, identify issues, and take corrective actions before problems escalate. This proactive approach fosters a culture of quality within organizations. Employees become more engaged when they see how their work contributes to overall improvement.
By integrating SPC into daily operations, companies encourage a shared responsibility for quality. Employees feel empowered to take ownership of their processes. They can identify variations and act accordingly. This collaboration leads to a more informed workforce and ultimately, a stronger organization.

Future Trends in SPC
The landscape of Statistical Process Control (SPC) is rapidly evolving, driven by advancements in technology. One of the most exciting trends is the integration of artificial intelligence (AI) and machine learning into SPC practices. These technologies can analyze vast datasets faster than ever, detecting patterns and anomalies that a human might miss. Imagine a world where your SPC charts update automatically, adapting to new data and providing real-time insights on process performance!
Moreover, SPC methodologies are evolving to tackle the complexities of modern manufacturing and service environments. Traditional SPC charts might struggle to keep up with the fast-paced, high-variation settings we see today. Enter adaptive control charts! These innovative charts adjust control limits based on current process behavior, providing a smarter approach to monitoring.
Another trend is the increased emphasis on training and education in SPC. As industries continue to adopt new technologies, there’s a growing need for skilled professionals who can harness these tools effectively. Organizations are investing in training programs to equip their employees with the knowledge necessary to interpret SPC charts and implement improvements confidently.
Educational institutions are also jumping in, offering specialized courses on SPC and its applications across various sectors. This renewed focus on training will prepare the next generation of industry professionals to tackle the challenges of tomorrow.
As we look to the future, embracing these advancements in SPC will empower organizations to maintain high-quality standards while adapting to the ever-evolving landscape of manufacturing and service delivery. For further insights, check out the recent trends in data analysis for financial forecasting 2024.
Understanding future trends in SPC can help organizations stay ahead of the competition. Explore the latest trends in data analysis for financial forecasting.

Conclusion
In summary, Statistical Process Control (SPC) is a vital tool for businesses aiming to enhance quality and efficiency. By enabling organizations to monitor processes in real time, SPC charts help identify variations and take corrective actions swiftly. This proactive approach not only minimizes defects but also fosters a culture of quality throughout the organization.
The integration of SPC into continuous improvement initiatives like Lean and Six Sigma further amplifies its effectiveness. With the rise of technology-driven advancements, such as AI and machine learning, the future of SPC looks bright. Organizations must prioritize training and education to ensure their workforce can leverage these tools effectively.
Ultimately, adopting SPC practices can lead to significant improvements in product quality, customer satisfaction, and operational efficiency. If you haven’t yet considered SPC for your organization, now is the time to explore its potential. Embrace the data-driven insights SPC offers and watch your processes thrive!
FAQs
What is an SPC chart?
Statistical Process Control (SPC) charts are graphical tools used to monitor and control processes over time. They display data points in relation to control limits. The chart helps identify trends and variations, allowing teams to determine if a process operates within acceptable limits. When data points fall outside these limits, it signals that the process may be experiencing special cause variation. Essentially, SPC charts are vital for assessing process stability and ensuring quality control in manufacturing and service industries.
How do I create an SPC chart?
Creating an SPC chart involves several key steps: – **Determine the measurement method:** Choose between variable (continuous) or attribute (discrete) data. – **Collect data:** Gather data consistently over time, ensuring enough points for analysis. – **Calculate control limits:** Establish the Upper Control Limit (UCL) and Lower Control Limit (LCL) using the average and standard deviation of your data. – **Plot data points:** Visualize the collected data on the chart, marking the control limits and center line. – **Analyze the chart:** Look for patterns, trends, or points outside the control limits, which may indicate the need for corrective actions.
What industries can benefit from using SPC?
SPC is a versatile tool applicable across various industries. Manufacturing is a prominent example, where it ensures product quality and consistency. In healthcare, SPC monitors patient outcomes and operational efficiency. Service industries also leverage SPC to track customer satisfaction metrics. Additionally, sectors like food production, logistics, and pharmaceuticals utilize SPC to enhance process control, reduce waste, and improve overall quality. Essentially, any industry that values quality management can benefit from implementing SPC charts.
What software can I use for SPC?
There are several popular software options available for creating SPC charts. Minitab is widely regarded for its robust statistical analysis capabilities, making it a favorite among quality professionals. Other options include Statgraphics, which offers a range of control chart types, and JMP, known for its interactive data visualization tools. Excel can also be used for basic SPC charting, though specialized software provides more advanced features and ease of use. Ultimately, the choice of software depends on the complexity of the data and specific user needs.
Please let us know what you think about our content by leaving a comment down below!
Thank you for reading till here 🙂
All images from Pexels