Introduction
Control charts are vital tools for monitoring process performance. They help identify variations in processes, which is crucial for improvement. In Lean and Six Sigma methodologies, control charts play a central role. This article aims to provide a clear roadmap for effectively implementing control charts in your organization.
For those looking to dive deeper into the realm of quality management, I highly recommend Control Chart for Quality Improvement. This book provides a comprehensive overview of how control charts can streamline your quality processes and enhance your overall efficiency.
Summary and Overview
Control charts are graphical tools used to track process behavior over time. They display data points and highlight trends, helping teams understand variations. Common types include X-bar charts for averages and R charts for range.
Statistical Process Control (SPC) is essential in both manufacturing and service sectors. SPC uses control charts to maintain process stability and improve quality. Many misconceptions exist regarding control charts. Some believe they only highlight problems, but they also reveal opportunities for enhancement.
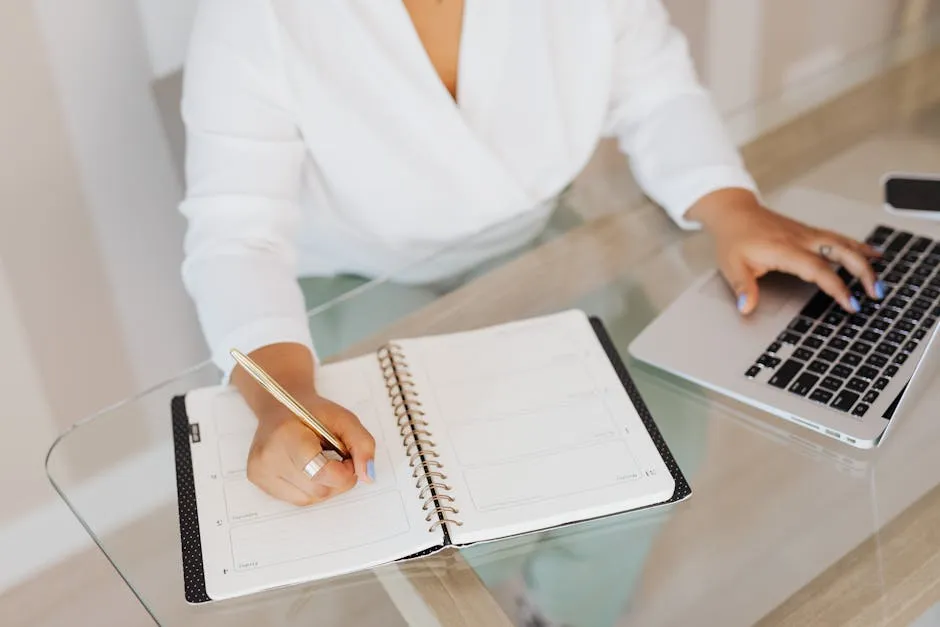
To further explore this topic, consider Statistical Process Control for Quality Improvement. It’s an excellent resource for anyone wanting to implement SPC effectively.
Understanding Control Charts
What are Control Charts?
Control charts are graphical tools used to monitor process variations. Their main purpose is to identify trends and shifts in data over time. Each chart consists of several components: a centerline representing the average, control limits to define acceptable variation, and data points plotted over time.
Different types of control charts serve various applications. For instance, X-bar charts track averages of samples, while R charts monitor the range of variation within those samples. Understanding these charts aids in maintaining quality and stability in processes.

If you’re serious about mastering these concepts, I recommend checking out The Lean Six Sigma Pocket Toolbook. It’s a handy guide packed with practical tools and insights!
The Importance of Statistical Process Control (SPC)
Statistical Process Control (SPC) is a method that utilizes control charts to monitor and analyze process stability. It plays a crucial role in quality management, helping organizations improve their processes and reduce variability. By applying SPC, companies can identify issues early, leading to timely interventions.
For example, a manufacturing plant might use SPC to monitor production quality. If a control chart indicates a trend towards lower quality, the team can investigate and make adjustments. Companies that effectively implement SPC often see improvements in product quality and operational efficiency, ultimately enhancing customer satisfaction.
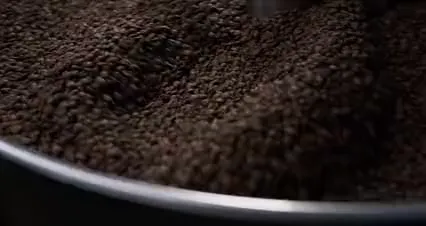
If you’re looking to up your game in quality management, grab a copy of Quality Control: A Practical Approach. It’s a fantastic resource for implementing effective quality strategies!
Process Variation
Common Cause vs. Special Cause Variation
Variation in processes can be categorized into two types: common cause and special cause. Common cause variation refers to the natural, expected fluctuations in processes. These variations are inherent and typically stable over time. For instance, slight differences in machine performance or material characteristics often fall under this category.
On the other hand, special cause variation arises from identifiable factors outside the normal operating conditions. This might include machine malfunctions or sudden changes in supplier quality. Recognizing the difference between these two types is vital for effective process improvement strategies. Addressing common causes often leads to incremental improvements, while tackling special causes may require more significant changes to processes.

Identifying and Analyzing Variation
Control charts are powerful tools for spotting variation in processes. To identify this variation, start by plotting your data over time. Look for patterns, trends, or shifts. Techniques like the moving average can also help smooth out fluctuations and reveal underlying trends.
Once you’ve identified variation, it’s crucial to analyze the data. Ask yourself: Is this variation due to common causes or special causes? Common cause variation is inherent and expected, while special cause variation stems from unusual events.
To address common cause variation, consider process improvements that reduce variability. This might involve standardizing procedures or retraining staff. For special cause variation, investigate the root cause and implement corrective actions swiftly. This approach ensures you maintain process stability and quality over time, leading to continuous improvement in your operations.
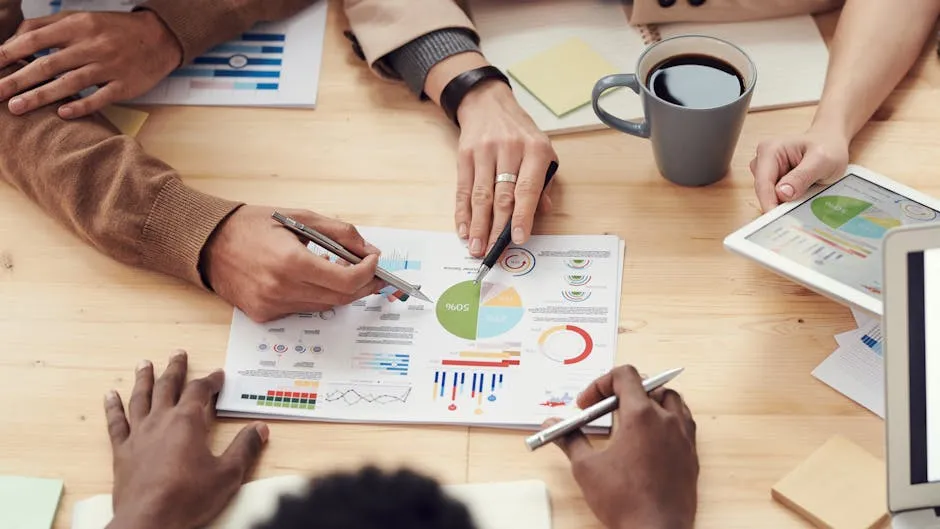
Implementing Control Charts
Selecting the Right Control Chart
Choosing the appropriate control chart is essential for effective monitoring. Start by considering the type of data you have. Is it continuous or discrete? Then, think about the characteristics of your process. For example, if you’re monitoring averages over time, an X-bar chart is suitable. Conversely, if you’re assessing proportions, a P chart may be the better choice.
Avoid common pitfalls, such as selecting a chart without understanding your data. This can lead to incorrect interpretations and wasted resources. Always ensure the chart aligns with your specific scenario. By doing so, you’ll enhance your ability to monitor processes accurately and drive improvements effectively.

For a more comprehensive understanding of these charts, consider adding Lean Six Sigma: Combining Six Sigma Quality with Lean Production Speed to your reading list! It’s a great resource for understanding the synergy between these methodologies.
Best Practices for Implementing Control Charts
Successful implementation of control charts involves several key steps. First, ensure your team is trained in data collection and chart interpretation. This foundational knowledge is vital for accurate monitoring.
Next, establish a routine for reviewing and updating your control charts. As new data comes in, adjust your charts to reflect current conditions. Continuous improvement is essential; regularly analyze the charts for insights and trends.
Finally, encourage a culture of feedback within your organization. This will help identify areas for refinement and ensure that control charts remain relevant and effective tools for process monitoring. By following these practices, you will foster a proactive approach to quality management and improvement.
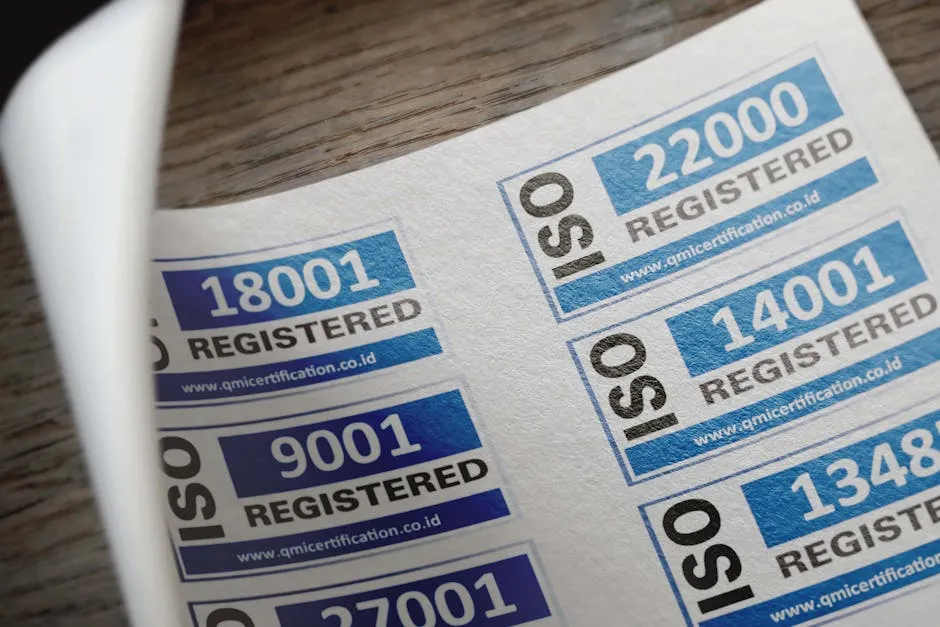
Analyzing Control Chart Data
Interpreting Control Charts
Reading control charts is straightforward once you grasp the basics. Each chart features a centerline that indicates the process average, with upper and lower control limits surrounding it. These limits define the expected range of variation.
Key indicators to monitor include trends, cycles, and out-of-control signals. A trend suggests a consistent increase or decrease in data points. If you notice points outside the control limits, this signals a potential issue that needs attention. For instance, if points repeatedly fall above the upper limit, it may indicate a significant process shift.
Actions based on interpretations can vary. If a trend appears, it might be time to investigate underlying causes. In contrast, if data points are scattered within limits, your process is likely stable. Keeping a close eye on these indicators ensures timely interventions for continuous improvement.
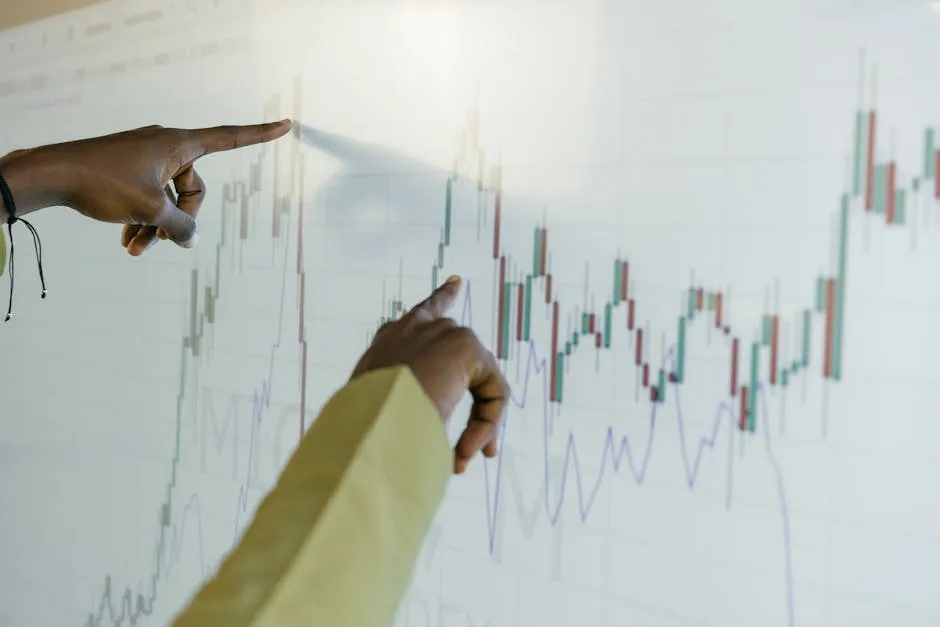
Continuous Improvement through Control Charts
Control charts serve as valuable guides for continuous improvement. They provide a visual feedback loop, enabling teams to analyze data effectively. Regularly reviewing control charts helps identify areas needing enhancement.
Feedback loops are essential for driving improvements. When teams assess data trends, they can pinpoint root causes of variation. This analysis leads to actionable strategies for process enhancement. Metrics such as process capability indices can measure the effectiveness of control chart implementation. By tracking these metrics, organizations can determine if their improvements yield the desired results.
Incorporating control charts into your improvement initiatives fosters a culture of data-driven decision-making. This approach not only enhances quality but also promotes a proactive mindset within teams.
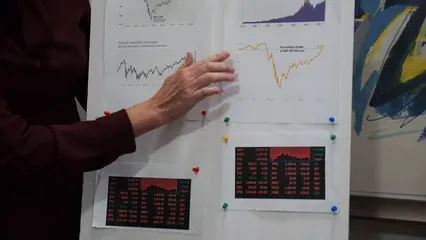
Conclusion
Control charts are crucial for achieving process excellence. They help identify variations and guide improvement efforts effectively. By understanding how to interpret these charts and harness their insights, you can drive meaningful change within your organization.
Adopting control charts as part of your continuous improvement strategy can enhance efficiency and quality. Embrace this powerful tool to ensure your processes remain robust and responsive to change.
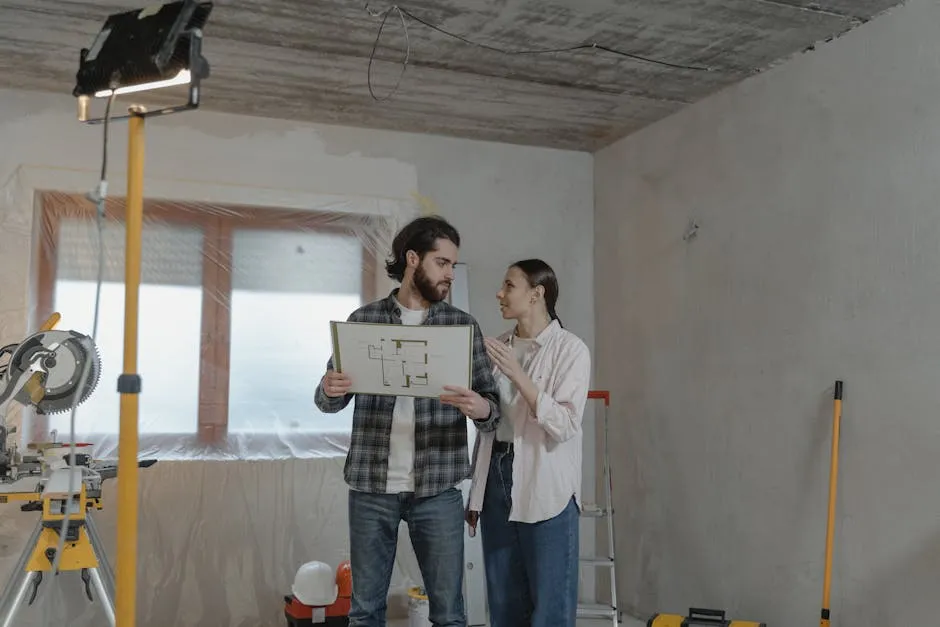
For a deeper dive into quality management, you might also find Quality Management Essentials to be a valuable resource!
FAQs
What is a control chart and why is it used?
Control charts are graphical tools that monitor process variations. They help identify if a process is stable or if there are changes that need attention. By plotting data points over time, control charts reveal trends and pinpoint variations, enabling teams to take corrective actions promptly.
How can I choose the right type of control chart for my process?
Selecting the right control chart starts with understanding your data type. If your data is continuous, consider X-bar or R charts. For categorical data, P or NP charts may be appropriate. Always align the chart type with your process characteristics to ensure effective monitoring.
What are the common mistakes when implementing control charts?
Common mistakes include choosing the wrong chart type and neglecting training. Failing to update charts regularly can also lead to outdated insights. To avoid these pitfalls, ensure proper training for your team and regularly review your control charts for relevance and accuracy.
How do control charts contribute to Six Sigma and Lean methodologies?
Control charts are essential in Six Sigma and Lean as they help visualize process performance. They enable teams to detect variations that affect quality. By integrating control charts, organizations can make data-driven decisions, leading to continuous improvement and enhanced efficiency.
Can control charts be used in service industries?
Absolutely! Control charts are applicable in service industries to monitor processes like customer support or order fulfillment. By tracking service metrics, organizations can identify trends and variations, ultimately leading to improved service quality and customer satisfaction.
Please let us know what you think about our content by leaving a comment down below!
Thank you for reading till here 🙂
For a deeper understanding of how control charts can enhance process management, check out this comprehensive guide on statistical process control control charts.
All images from Pexels