Introduction
Manufacturing plants run on data. But what if that data is like a foreign language? Enter descriptive statistics! This powerful tool transforms complex information into understandable insights. Imagine navigating a bustling factory floor with a map that highlights key patterns and performance metrics. That’s the magic of descriptive statistics.
The purpose of this article is to illuminate the significance of descriptive statistics in manufacturing plants. With increasing reliance on data-driven decisions, manufacturers need to understand operational efficiency. Descriptive statistics provide that understanding, offering clarity amid the chaos of numbers.
In today’s fast-paced manufacturing environment, every decision counts. From quality control to production optimization, the ability to analyze data effectively can lead to significant improvements. Descriptive statistics help managers monitor trends, assess performance, and make informed choices. They stand as a cornerstone for operational success, fueling continuous improvement.

To dive deeper into the world of data analysis, I highly recommend Descriptive Statistics: A Practical Guide for Researchers. It’s a great way to get a comprehensive understanding of the concepts that will be discussed throughout this article!
Throughout this article, readers can expect to learn about the basic concepts of descriptive statistics, its vital role in manufacturing, and practical examples that illustrate its application. We will break down complex terms into bite-sized pieces, ensuring clarity and accessibility. By the end, you’ll be equipped with the knowledge to harness descriptive statistics for enhanced manufacturing performance.
Understanding Descriptive Statistics
What are Descriptive Statistics?
Descriptive statistics are the unsung heroes of data analysis. They summarize and organize data, transforming raw figures into meaningful insights. Picture it as a magnifying glass that highlights the essential features of a dataset, making it more digestible.
At its core, descriptive statistics encompass several key components. Measures of central tendency—mean, median, and mode—offer a snapshot of the data’s typical values. Meanwhile, measures of dispersion—like range, variance, and standard deviation—help gauge the variability within the dataset. Together, they provide a comprehensive overview of the data’s structure.
For instance, if a manufacturing plant collects data on production output, descriptive statistics can reveal the average output per shift, the most common output level, and the variability in production. This insight allows managers to identify trends, spot anomalies, and enhance operational efficiency.

To further enhance your data analysis skills, consider reading The Data Warehouse Toolkit: The Definitive Guide to Dimensional Modeling. This book dives into the intricacies of data organization, which is crucial for effective descriptive statistics.
Importance of Descriptive Statistics in Manufacturing
Descriptive statistics play a pivotal role in decision-making within manufacturing environments. By providing a clear picture of operational performance, they empower managers to evaluate efficiency and identify areas for improvement. Let’s consider a few examples.
In quality control, descriptive statistics can track defect rates. By analyzing data over time, managers can determine if defect rates are improving or worsening. This insight allows for timely interventions, ensuring product quality remains high.
Another practical application lies in performance evaluation. For instance, if a factory measures the time taken to complete specific tasks, descriptive statistics can highlight average completion times and identify outliers. This information can pinpoint bottlenecks in the process, leading to targeted improvements.
Furthermore, descriptive statistics aid in resource allocation. By understanding production trends, managers can optimize workforce deployment and material usage. For example, if data reveals increased demand for a specific product line, resources can be shifted accordingly to meet that demand without overextending operations.
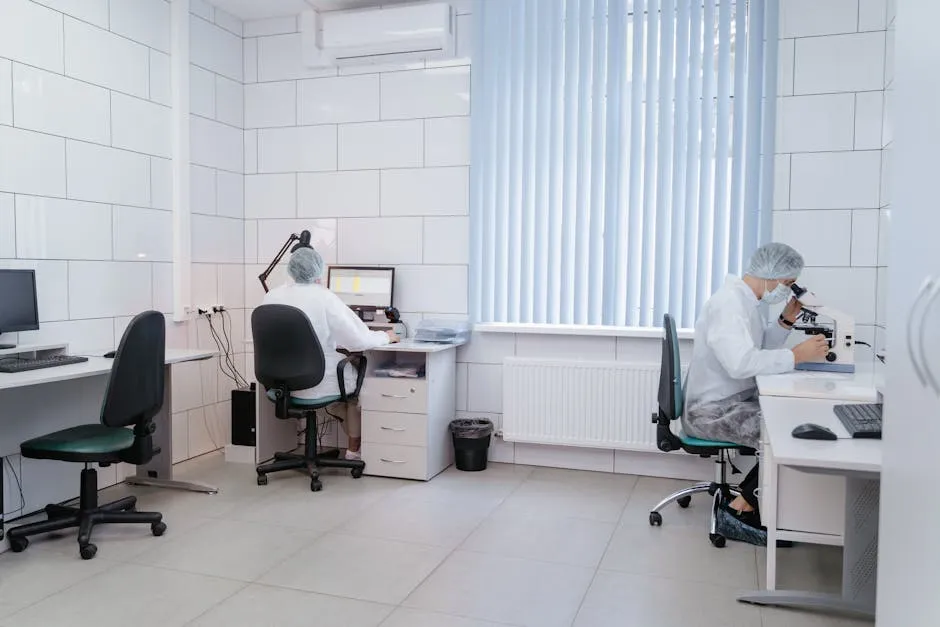
To deepen your understanding of data analysis, I suggest checking out A Beginner’s Guide to Data Analysis. It’s a fantastic resource for those just starting on their data journey!
In summary, descriptive statistics empower manufacturing plants to make informed decisions, optimize operations, and enhance overall performance. By leveraging data effectively, manufacturers can stay ahead of the competition and continuously improve their processes.
Key Measures of Descriptive Statistics
Measures of Central Tendency
Mean
The mean is the average of a data set. To compute it, add all values and divide by the number of entries. In a manufacturing context, consider the average production output per day. If a factory produces 100, 120, and 80 units on three consecutive days, the mean output is (100 + 120 + 80) / 3 = 100 units. This metric provides insight into overall production efficiency.

For those interested in enhancing their skills in Python for data analysis, you should definitely check out Python for Data Analysis: Data Wrangling with Pandas, NumPy, and IPython. It’s a fantastic way to gain practical skills applicable in the manufacturing realm!
Median
The median is the middle value in a sorted list. It’s especially useful for understanding data distributions that may be skewed. For example, if a manufacturing team tracks the time taken to complete a task across five shifts, recorded times in minutes might be: 30, 32, 28, 50, and 29. When sorted, these become 28, 29, 30, 32, and 50. The median time is 30 minutes, indicating that half the shifts took less than this time, which helps in evaluating performance and identifying outliers.
The median is a crucial measure in statistics, especially in contexts like salary analysis. For more insights, check out the statistics Poland median salary 2024.
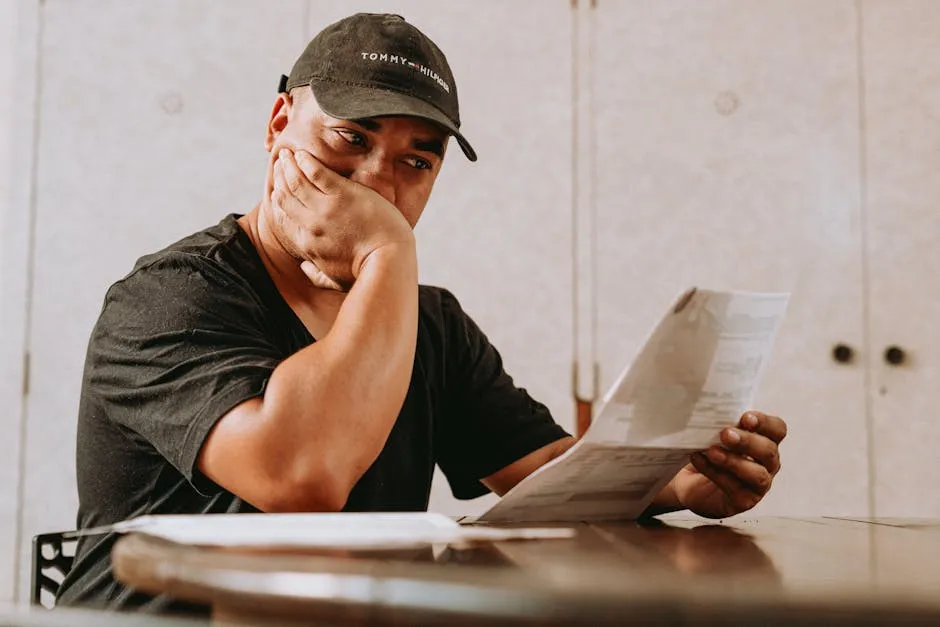
Mode
The mode identifies the most frequently occurring value in a dataset. In manufacturing, it can reveal trends in production. For instance, if a factory produces the following quantities of different products in a week: 10, 12, 10, 14, 10, and 11, the mode is 10. This indicates that the factory produced this quantity most often, guiding inventory management decisions and production planning.
Measures of Dispersion
Range
The range highlights the difference between the highest and lowest values in a dataset. In a manufacturing scenario, assessing the range of production times can help identify variability. If production times over a week are recorded as 25, 30, 28, 31, and 29 minutes, the range is 31 – 25 = 6 minutes. This measure indicates how consistent the production times are, which is crucial for operational efficiency.
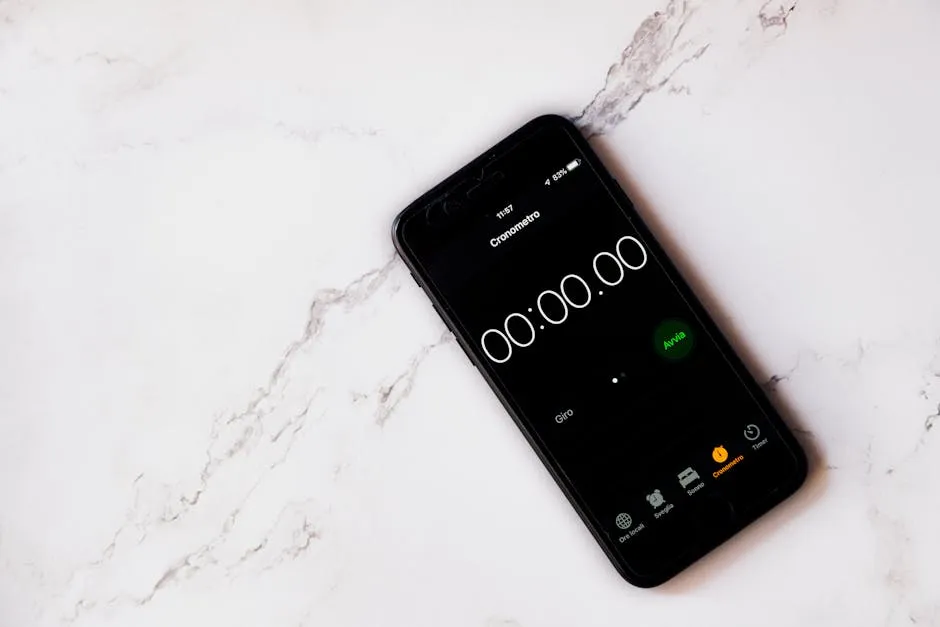
Variance and Standard Deviation
Variance measures how far each number in the dataset is from the mean, while the standard deviation is the square root of the variance. Both metrics provide insights into data variability. For example, if a manufacturing plant has product weights recorded as 10, 12, 10, 14, and 10 grams, the mean is 12 grams. The variance helps in understanding how much these weights deviate from the average. A low variance indicates stability in product weight, which is essential for quality control.
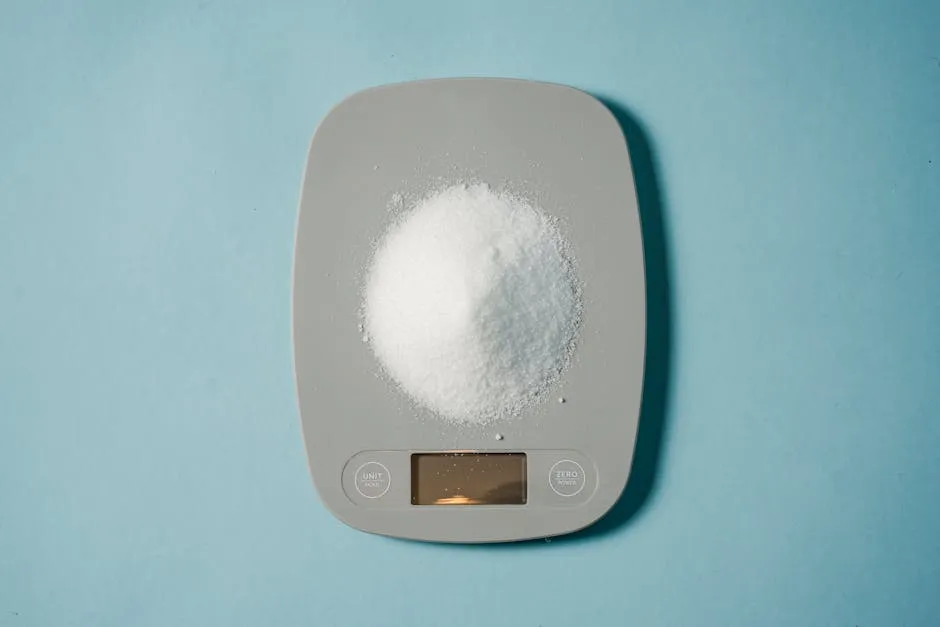
For a more in-depth understanding of data visualization techniques, consider The Visual Display of Quantitative Information. This book helps you master the art of presenting data visually, making your statistics all the more impactful!
Visualization Techniques
Visualization tools are the cherry on top of descriptive statistics. They make complex data easier to digest. Common visual aids include histograms, box plots, and bar charts.
Histograms display the distribution of production times or costs. They reveal patterns, such as whether production times cluster around a specific value or if they are spread out. This visual representation allows managers to quickly assess performance and identify trends.
Box plots provide insights into the spread and skewness of data. They show the median, quartiles, and potential outliers in production times. If a box plot reveals many outliers, it could indicate underlying issues in the manufacturing process that need attention.
Bar charts are ideal for comparing different categories, such as production output across various shifts. They can help visualize differences in performance, making it easier to spot trends over time.
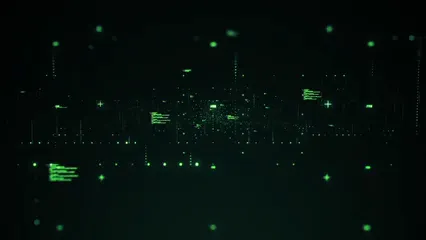
By leveraging these visualization techniques, manufacturing managers can make data-driven decisions. Clear visuals provide immediate insights, facilitating discussions around performance optimization and operational efficiency. Each tool offers unique perspectives, helping to foster a culture of continuous improvement within the plant.
Production Analysis
Descriptive statistics are invaluable for analyzing production efficiency in manufacturing plants. They help managers understand how well production processes are performing. By applying these statistics, plants can identify trends, pinpoint bottlenecks, and optimize workflows.
For example, consider a factory that produces widgets. By collecting data on production rates, managers can calculate the average output over a week. If the average output is significantly lower than expected, it may indicate issues with machinery or workforce efficiency. A real-world case from a manufacturing plant in Michigan found that, after applying descriptive statistics to their production data, they discovered that a particular machine had downtime affecting output. By addressing this issue, they increased production by 20% within a month.
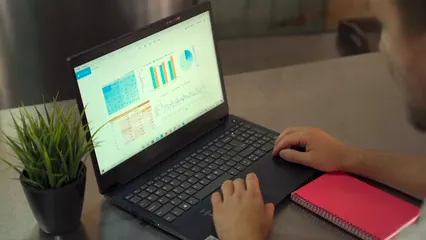
Another case study involves a beverage manufacturer that utilized descriptive statistics to analyze the time taken for each production stage. They discovered that the bottling phase consistently lagged behind others. By reallocating resources and optimizing the bottling process, they improved overall production efficiency, leading to a quicker turnaround time for their products.
Inventory Management
Descriptive statistics play a crucial role in inventory analysis by providing insights into stock levels and turnover rates. This data enables manufacturing plants to maintain optimal inventory levels, reducing costs and avoiding stockouts.
For instance, a car manufacturing plant may track the inventory of spare parts. By calculating the average turnover rate of these parts, managers can determine how often inventory needs replenishing. If the data reveals that certain parts have a low turnover rate, the plant can consider reducing the stock of those items while increasing orders for high-demand components.
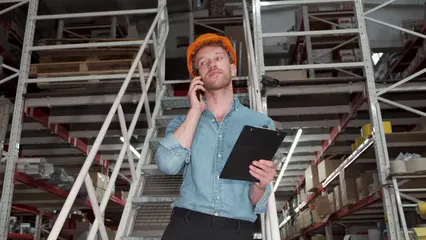
A notable example comes from a food processing company that employed descriptive statistics to analyze their inventory data. They found that seasonal demand for certain snacks fluctuated significantly. By adjusting their inventory levels based on statistical trends, they minimized waste and ensured they had enough products to meet consumer demand during peak seasons. This strategy not only saved costs but also improved customer satisfaction.
Workforce Productivity
Evaluating employee performance and productivity is another area where descriptive statistics shine. By measuring metrics such as output per hour or task completion rates, managers can identify high performers and those needing support.
Consider a textile manufacturing plant that tracks the number of garments produced by each worker daily. By calculating the mean output across shifts, managers can identify which teams are performing exceptionally well. Conversely, if a particular shift consistently underperforms, it may indicate issues such as insufficient training or morale problems.
One example comes from a furniture factory that analyzed its workforce productivity using descriptive statistics. They discovered that the average output varied significantly among employees. After further analysis, they realized that those with more experience produced higher quality goods faster. By implementing targeted training programs for newer employees, the factory managed to elevate overall productivity by 15% within three months. This approach not only benefited the company but also fostered a culture of continuous improvement among the workforce.

To further improve your understanding of workforce analytics, I recommend The Essentials of Data Science: A Practical Guide to Data Analysis. This book provides concrete examples and methodologies for analyzing workforce data effectively!
Best Practices for Implementing Descriptive Statistics in Manufacturing
Data Collection
In the manufacturing sector, robust data collection is non-negotiable. It’s the foundation upon which insightful analysis is built. Think of it as laying the groundwork for a skyscraper; if the base is weak, the entire structure is compromised.
Effective data collection methods ensure accuracy and reliability. Use automated data collection tools to minimize human error. Sensors and IoT devices can gather real-time data, providing a continuous flow of information. This technology can help track everything from machine performance to employee productivity.
However, pitfalls lurk in the shadows. Bias in sampling can skew results. Always strive for random sampling to capture a true representation of your processes. Incomplete data is another common foe. A missing piece here and there can lead to significant misinterpretations. Make sure data collection covers all necessary variables thoroughly. Regular audits of the data collection process can help identify gaps and inconsistencies.

Analysis Techniques
Once data is collected, it’s time to roll up your sleeves and analyze it! Here, descriptive statistics come into play, revealing insights that guide decision-making. Best practices include using software tools like SPSS Statistics for Dummies, R, or Python for data analysis. These platforms offer powerful capabilities for summarizing data, calculating averages, and identifying trends.
Utilize measures of central tendency—mean, median, and mode—to get a sense of your data’s typical values. Measures of dispersion, such as variance and standard deviation, will help you understand the variability within your manufacturing processes. For example, if your production times have a low standard deviation, you can confidently predict future performance.
Don’t shy away from visual tools such as histograms and box plots. They can transform raw numbers into compelling visuals that make your data story easier to understand. Employing these tools not only enhances clarity but also encourages team engagement in discussions around performance metrics.

Continuous Improvement
Descriptive statistics play a crucial role in continuous improvement. By regularly analyzing operational data, manufacturers can identify trends and areas for enhancement. Imagine a factory that monitors its production output weekly. By analyzing this data over time, it can spot patterns—whether production is consistently lower on Mondays or if certain machines frequently underperform.
These insights allow for proactive adjustments. For example, if data reveals that a specific machine often requires maintenance, scheduling regular check-ups can prevent costly downtimes. This practice not only enhances efficiency but also motivates a culture of continuous improvement among employees. After all, who doesn’t want to work in a place that’s always getting better?
Encourage a feedback loop where insights from data analysis lead to actionable changes. Regularly revisit your data collection and analysis methods to ensure they evolve alongside your manufacturing processes. Continuous improvement is not just a buzzword; it’s the lifeblood of a successful manufacturing operation.

FAQs
What is the difference between descriptive and inferential statistics?
Descriptive statistics focus on summarizing and presenting data characteristics. They help provide quick insights into the dataset without making predictions or generalizations. For example, if a manufacturing plant analyzes its production output for the last month, the average output or the most common output level are descriptive statistics. On the other hand, inferential statistics aim to make inferences about a larger population based on a sample. For example, if a plant sampled production data from 50 shifts to predict the average output for all shifts, this would fall under inferential statistics. The key difference lies in the scope: descriptive statistics describe the sample at hand, while inferential statistics draw conclusions beyond that sample, often involving uncertainty. In manufacturing, both types of statistics are vital. Descriptive statistics help understand current operations, while inferential statistics guide future decisions based on past data.
Please let us know what you think about our content by leaving a comment down below!
Thank you for reading till here 🙂
All images from Pexels