Introduction
Forecasting trends in manufacturing is like predicting the weather. Accurate forecasts can save companies from costly overproduction or stockouts. In today’s fast-paced world, businesses must stay ahead of the curve. They need to anticipate market fluctuations and customer demands effectively. That’s where time series analysis comes into play.
Time series analysis is a powerful statistical tool used to analyze data points collected over time. This method helps in identifying patterns, trends, and seasonal variations. By using historical data, manufacturers can make data-driven decisions to enhance their operational efficiency. If you’re looking to dive deeper into this topic, consider picking up Time Series Analysis: Forecasting and Control by Charles S. Tapiero. It’s a must-read for anyone serious about mastering forecasting techniques!
Accurate forecasting is crucial for several reasons. First, it aids in inventory management. By predicting demand, manufacturers can optimize their stock levels, reducing excess inventory and minimizing carrying costs. Second, it supports cost reduction efforts. When businesses can anticipate production needs, they can allocate resources more effectively, leading to decreased operational expenses. Finally, meeting customer demand is paramount. Satisfied customers are repeat customers. By forecasting trends accurately, businesses can ensure they have the right products available at the right time.
This article will cover essential aspects of time series analysis, including its definition, key components, and its significance in manufacturing. We will also discuss challenges and benefits, methodologies for implementation, and real-world applications. Let’s dive into the fascinating world of forecasting trends with time series analysis!

Understanding Time Series Analysis
What is Time Series Analysis?
Time series analysis refers to the statistical technique used to analyze time-ordered data points. It helps in understanding how variables evolve over time. This method involves collecting data at regular intervals, allowing analysts to observe trends and patterns that develop.
Time-stamped data is vital for analyzing historical trends. Each data point is linked to a specific time, enabling manufacturers to observe changes over periods. For example, analyzing monthly sales data can provide insights into seasonal fluctuations, helping businesses prepare for peak demand. If you’re keen on learning more about the underlying statistics, check out The Art of Statistics: Learning from Data by David Spiegelhalter. It’s a fantastic resource!
Key Components of Time Series Analysis
To grasp time series analysis fully, it’s essential to understand its key components:
- Trend: This refers to the long-term movement or direction of the data. Identifying trends helps businesses understand whether their performance is improving or declining over time.
- Seasonality: These are patterns that repeat at regular intervals, such as increased demand during holidays or specific seasons. Recognizing seasonal patterns allows manufacturers to adjust their production schedules accordingly.
- Cyclicity: This involves fluctuations that occur over extended periods but aren’t strictly seasonal. These cycles can be influenced by economic changes, making them crucial for long-term planning.
- Irregularity: This refers to random noise in the data, which can obscure patterns. Identifying and accounting for irregularities is vital for accurate forecasting.
Understanding these components enables manufacturers to develop robust forecasting models. By analyzing trends, seasonality, cyclicity, and irregularities, businesses can gain valuable insights to support their decision-making processes. With time series analysis, manufacturers can navigate the complexities of their industry with confidence.

Importance of Time Series Analysis in Manufacturing
Challenges in Manufacturing Forecasting
Manufacturing forecasting is no walk in the park. It’s more like trying to juggle flaming torches while riding a unicycle. Common challenges abound, making accurate predictions a tricky endeavor.
One major hurdle is fluctuating demand. Imagine a company producing winter jackets. As summer rolls in, demand dives faster than a lead balloon. If a manufacturer misjudges this shift, they might end up with a warehouse full of jackets just in time for beach season. Not ideal!
Seasonal trends add another layer of complexity. Take the holiday season, for instance. Many businesses see a spike in demand, while others experience a drop. If a toy manufacturer fails to forecast the holiday rush, they risk disappointing eager children everywhere. The lesson? Companies must stay alert to these seasonal changes to avoid missed sales opportunities.
A classic example is ABC Manufacturing, which specializes in consumer electronics. They faced soaring inventory costs because their production often didn’t match customer demand. This mismatch led to frustrating stockouts or excess inventory. The result? Missed sales opportunities and unhappy customers. Not a great recipe for success!
Furthermore, varying lead times for raw materials complicate matters. If suppliers suddenly delay shipments, manufacturers might find themselves scrambling to adjust production schedules. This chaos can lead to inefficient operations and increased costs.
In summary, the challenges faced in manufacturing forecasting are substantial. Fluctuating demand, seasonal trends, and changing lead times can throw a wrench in even the most carefully crafted plans. Accurate forecasting is crucial to navigate these turbulent waters successfully.

Benefits of Time Series Analysis
Now that we’ve tackled the challenges, let’s explore the benefits of time series analysis. This powerful tool can be the knight in shining armor for manufacturers looking to enhance their forecasting accuracy.
First and foremost, time series analysis improves forecasting accuracy. By examining historical data, manufacturers can identify patterns and trends that inform future demand. This insight helps optimize inventory management, reducing excess stock and minimizing carrying costs. Imagine a world where warehouses are stocked just right, without overflowing or running dry! For a more in-depth understanding of these principles, consider reading The Data Warehouse Toolkit: The Definitive Guide to Dimensional Modeling by Ralph Kimball. It’s a classic in the field!
Next up is cost savings. With enhanced forecasting accuracy, manufacturers can optimize production schedules. This means fewer unnecessary overtime hours, reduced waste, and better resource allocation. Who doesn’t love saving a few bucks while increasing efficiency?
Moreover, time series analysis allows for better alignment of production with market demand. Companies can adjust their manufacturing processes based on accurate forecasts, ensuring they meet customer needs without overcommitting resources. This adaptability can lead to improved customer satisfaction and loyalty, crucial for long-term success.
In short, the benefits of time series analysis in manufacturing are hard to ignore. Enhanced forecasting accuracy, cost savings, and improved alignment with market demand create a powerful trifecta. By leveraging these advantages, manufacturers can navigate the complexities of their industries with confidence and agility.

Methodology for Time Series Analysis in Manufacturing
Data Collection
Gathering the right data is foundational for effective time series analysis in manufacturing. Several types of data are necessary to create a robust forecasting model.
Historical sales data is paramount. This data reveals past performance and trends, providing a solid foundation for predictions. For instance, if a manufacturer tracks monthly sales of a specific product, they can identify seasonal patterns that inform future production. If you’re interested in exploring more about data analysis, grab a copy of Python for Data Analysis: Data Wrangling with Pandas, NumPy, and IPython by Wes McKinney. It’s a fantastic resource for anyone looking to improve their data skills!
Production data is equally important. Analyzing past production levels helps manufacturers understand their capacity and efficiency. By comparing production data with sales, manufacturers can gauge whether their output aligns with demand.
Data collection methods vary. Many companies utilize Enterprise Resource Planning (ERP) systems to gather historical data automatically. These systems streamline data collection, ensuring consistency and accuracy. Additionally, surveys and customer feedback can provide valuable insights into changing preferences and demand.
Organizing this data is crucial for analysis. Manufacturers should ensure that all data is time-stamped and categorized appropriately. This organization allows for meaningful analysis and enhances the accuracy of forecasts.
In conclusion, effective data collection is a cornerstone of time series analysis in manufacturing. By gathering and organizing relevant historical sales and production data, manufacturers can unlock powerful insights that drive informed decision-making.

Data Preprocessing
Data preprocessing acts like a warm-up routine before the heavy lifting of time series analysis. It’s crucial to get it right to avoid any forecast flops. First, let’s tackle the pesky issue of missing values. Imagine you’re piecing together a puzzle, only to find a few critical pieces are MIA. Filling in these gaps is essential. Techniques like interpolation can estimate missing data based on existing values, ensuring your dataset remains robust.
Next up, we have outliers. These are the data points that stand out like a sore thumb. They can skew your analysis, leading to inaccurate forecasts. A good practice is to use methods like the Z-score to identify and remove these anomalies. This helps in presenting a clearer picture of your data’s behavior.
Maintaining data quality is paramount. Clean data leads to accurate forecasts, while dirty data leads to errors and confusion. Think of it as polishing your crystal ball; the clearer the view, the better the predictions. Ensuring data consistency, accuracy, and completeness lays a solid foundation for the forecasting models.
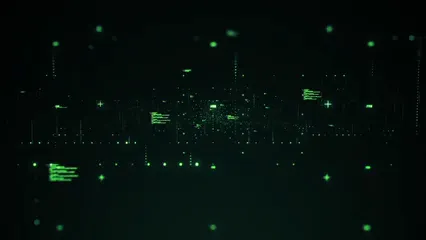
Model Selection
Choosing the right time series model is like picking the perfect outfit for a first date—it can make all the difference! Let’s explore some popular models used in manufacturing forecasting:
- ARIMA (Autoregressive Integrated Moving Average): This model is a classic choice. It captures trends and relationships in univariate data. Perfect for when you want to understand past behaviors and predict future outcomes.
- SARIMA (Seasonal ARIMA): When your data has seasonal aspects—think holiday sales—SARIMA is your go-to. It extends ARIMA by adding seasonal terms, allowing it to handle patterns that repeat over time.
- Exponential Smoothing: This model applies decreasing weights to past observations. It’s particularly useful for datasets with trends and seasonality. It helps you smooth out data to get a clearer view of what’s happening.
- TBATS (Trigonometric, Box-Cox Transformation, ARMA Errors, Trend, and Seasonal Components): A mouthful, right? But TBATS is fantastic for data with multiple seasonal patterns. It can handle complex seasonality, making it ideal for diverse manufacturing environments.
When selecting a model, consider your data characteristics. Is it seasonal? Does it exhibit trends? Test different models and validate their performance to ensure you pick the best fit for your needs. For those interested in diving deeper into forecasting methodologies, Forecasting: Methods and Applications by Spyros Makridakis is an excellent choice!

Model Validation and Implementation
Once you’ve selected a model, it’s time to validate its performance. Think of it as giving your model a test run before it hits the big stage. Key techniques include Mean Absolute Error (MAE) and Root Mean Square Error (RMSE). These metrics will help you assess how well your model predicts compared to actual values. Lower error rates mean better accuracy—simple as that!
After validation, the next step is integrating your forecasting model into production planning systems. This process involves ensuring that your model works seamlessly with existing software and workflows. Create a user-friendly interface for your team, so they can easily access and interpret the forecasts. Training sessions can be beneficial here, helping everyone get up to speed.
By following these steps, you can effectively implement a robust forecasting solution that enhances manufacturing efficiency. With the right model in place, you’ll be better equipped to make data-driven decisions, optimize inventory, and align production with market demand.

Case Study 1: ABC Manufacturing
ABC Manufacturing specializes in consumer electronics. Like many companies, they faced significant challenges in forecasting production needs. Their inventory costs were skyrocketing, and mismatches between customer demand and production output led to missed sales opportunities. The company recognized the need for a more data-driven approach to tackle fluctuating demand, seasonal trends, and varying lead times.
To address these issues, ABC Manufacturing implemented time series analysis. They began by gathering historical production and sales data. After cleaning and organizing the data, they selected several forecasting models, including ARIMA and Exponential Smoothing. The company validated the models using statistical measures like Mean Absolute Error.
As a result, ABC Manufacturing achieved significantly improved forecasting accuracy. This led to reduced inventory costs and minimized stockouts. The streamlined supply chain allowed for better alignment of production with actual demand. Ultimately, the company gained a competitive advantage by quickly adapting to market changes. This case demonstrates the importance of predicting future trends.
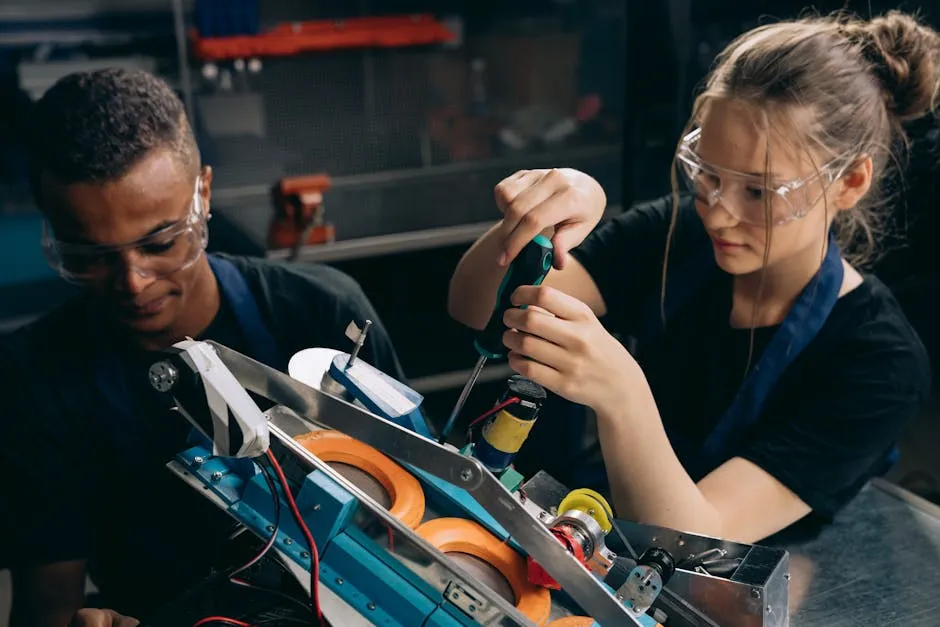
Case Study 2: Walmart
Walmart is a giant in retail, known for its efficient supply chain and inventory management. They use time series forecasting extensively for demand and inventory management. By analyzing historical sales data, Walmart can predict future demand patterns. This approach helps them maintain optimal inventory levels across their vast network of stores.
When demand spikes, such as during holiday seasons, Walmart can adjust its inventory accordingly. The implementation of time series analysis allows them to anticipate purchasing trends, ensuring products are available when customers want them. This accuracy translates into fewer stockouts and excess inventory.
The outcomes for Walmart have been substantial. Improved supply chain efficiency has led to significant cost savings. Their ability to forecast demand accurately has enhanced customer satisfaction, as shelves remain stocked with popular items. In a competitive retail environment, precise forecasting is a game changer. If you’re interested in learning more about business analytics, consider checking out Business Analytics: Data Analysis & Decision Making by S. Christian Albright and Wayne L. Winston. It’s a great resource for those looking to improve their analytical skills!
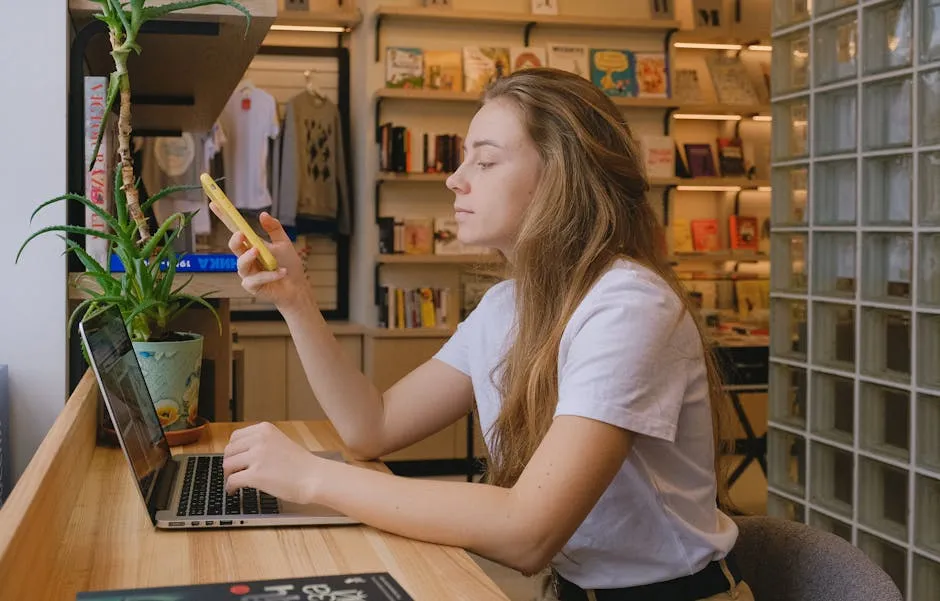
Additional Examples from Other Industries
Time series forecasting isn’t limited to manufacturing and retail. Various industries have successfully applied this technique. In finance, institutions like Goldman Sachs leverage time series analysis for risk management and market predictions. Similarly, energy companies utilize it for electricity demand forecasting. In healthcare, time series data helps predict patient admissions, optimizing resource allocation. Each of these examples demonstrates the versatility and importance of time series analysis across sectors.
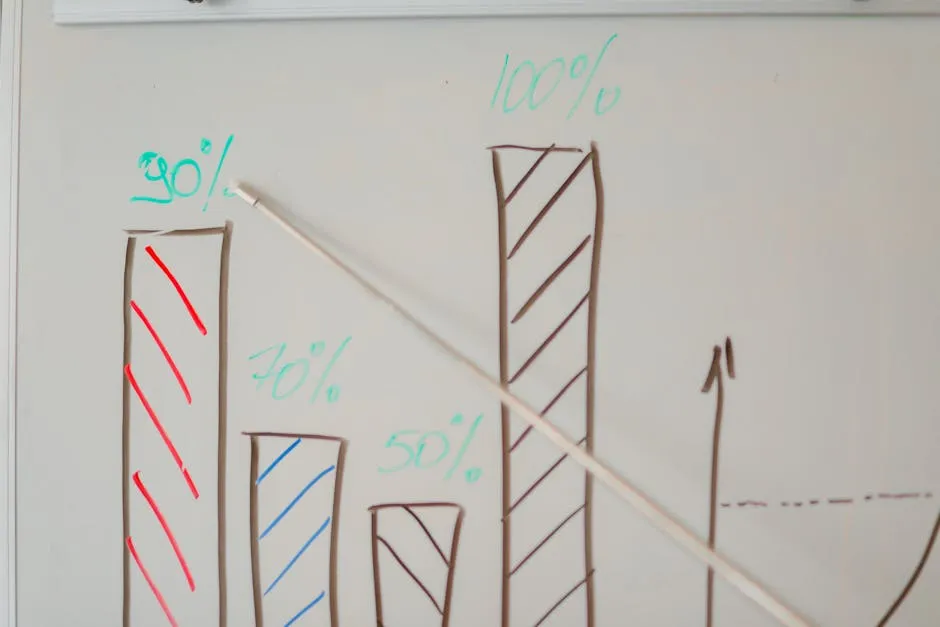
Future Trends in Time Series Analysis for Manufacturing
Emerging Technologies
The future of time series analysis in manufacturing is bright, thanks to emerging technologies. Machine learning and artificial intelligence are making significant inroads into forecasting practices. These technologies can analyze vast datasets much faster than traditional methods, uncovering patterns that humans might overlook. By integrating AI, manufacturers can enhance the accuracy of their forecasts, adapting to market dynamics in real-time. Interested in machine learning? Check out Machine Learning Yearning by Andrew Ng. It’s a fantastic read for anyone looking to grasp the fundamentals!
Real-time data analysis is another game-changing trend. With the Internet of Things (IoT) becoming more prevalent, manufacturers can gather data continuously from production lines. This real-time input allows for immediate adjustments to production schedules based on current demand. Imagine a factory that adjusts its output on-the-fly, leading to better resource use and waste reduction. This level of responsiveness is becoming increasingly feasible.
As these technologies evolve, manufacturers will benefit from enhanced predictive capabilities. The combination of machine learning, real-time data, and advanced analytics will empower companies to make faster, more informed decisions. The landscape of manufacturing will be revolutionized, with data-driven strategies leading the way to greater efficiency and competitiveness.
In conclusion, the integration of these emerging technologies into time series analysis is set to redefine manufacturing forecasting. Companies that embrace these advancements will likely experience improved operational efficiencies and better alignment with market demands. The future is here, and it promises to be data-rich and insightful.

The Role of Big Data
Big data analytics revolutionizes time series analysis in manufacturing. It transforms raw data into valuable insights. By analyzing vast amounts of data, manufacturers can identify hidden patterns. This leads to more accurate forecasting and better decision-making.
The quality of time series analysis improves significantly with big data. Traditional methods often rely on limited datasets. In contrast, big data allows for the integration of diverse information sources. This includes sales figures, production schedules, and even social media trends. By combining these datasets, manufacturers gain a holistic view of market dynamics. This comprehensive perspective enables businesses to anticipate changes and adapt strategies accordingly.
Leveraging diverse data sources is crucial for better insights. Data can come from various channels, such as IoT devices, customer interactions, and supply chain operations. Each source adds a layer of depth to the analysis. For instance, real-time data from sensors on production lines can highlight immediate fluctuations in demand. This immediacy allows manufacturers to react swiftly, optimizing inventory levels and reducing waste.
Additionally, big data analytics enhances predictive capabilities. Machine learning algorithms can analyze historical patterns and forecast future trends. These models learn from the data, continuously improving their accuracy. This adaptability is vital in the ever-changing manufacturing landscape, where consumer preferences shift rapidly.
In summary, big data analytics empowers manufacturers to refine their time series analysis. By harnessing diverse data sources, businesses can make informed decisions. The result is enhanced forecasting accuracy and operational efficiency, ultimately leading to greater competitiveness in the market.

FAQs
What is time series forecasting?
Time series forecasting is a statistical technique used to predict future values based on historical data. It analyzes time-ordered data points to identify trends, seasonality, and patterns. This method is particularly relevant in manufacturing, as it helps businesses anticipate demand, optimize inventory, and align production with market needs.
How can time series analysis improve inventory management?
Accurate forecasts derived from time series analysis lead to better inventory control. By understanding demand patterns, manufacturers can optimize stock levels, reducing both stockouts and excess inventory. This efficiency minimizes carrying costs and improves cash flow, ensuring that the right products are available at the right time.
What are the common challenges in implementing time series analysis?
Implementing time series analysis can present challenges such as ensuring data quality, selecting the appropriate forecasting model, and addressing missing values or outliers. Additionally, businesses must be vigilant about changing market conditions that can affect data patterns. Overcoming these obstacles requires careful planning and robust data management strategies.
Can small manufacturers benefit from time series analysis?
Absolutely! Time series analysis is beneficial for manufacturers of all sizes. Small manufacturers can leverage this technique to enhance forecasting accuracy, improve inventory management, and make informed decisions. By adopting time series analysis, even small businesses can compete effectively in the market, optimizing their operations and driving growth.
Please let us know what you think about our content by leaving a comment down below!
Thank you for reading till here 🙂
All images from Pexels