Introduction
In today’s manufacturing landscape, data reigns supreme. Statistics play a pivotal role in transforming raw data into actionable insights. Companies can optimize processes, enhance quality, and boost efficiency with the right statistical tools. But wait, there’s more! The Fourth Industrial Revolution, or Industry 4.0, has taken this a step further. It’s not just about collecting data anymore; it’s about leveraging it in real-time for smart decision-making.
Imagine a factory where machines talk to each other, and data flows seamlessly to inform every aspect of production. That’s the magic of Industry 4.0! Thanks to advanced analytics and IoT devices, businesses can monitor operations, predict trends, and improve overall performance. No longer are manufacturers flying blind; statistics now guide their way.
This article aims to explore the various applications of statistics in manufacturing. We’ll show how data-driven decision-making can lead to improved efficiency, enhanced quality, and smarter choices. Whether you’re a plant manager or a curious enthusiast, you’ll discover the transformative power of statistics in the manufacturing realm.

Importance of Statistics in Manufacturing
Statistics is not just an academic exercise; it’s a lifeline for modern manufacturing. Why? Because the ability to analyze data effectively can spell the difference between success and failure. To start, data analysis helps identify trends and makes informed decisions. Manufacturers can react proactively to changes in demand or detect issues before they escalate.
In recent years, there’s been a significant shift towards data-driven decision-making. Gone are the days of relying solely on gut feelings or historical practices. Instead, companies are harnessing the power of statistical methods to guide their choices. From quality control to production planning, statistics are integral to optimizing processes and reducing waste.
Integrating statistical methods into manufacturing processes comes with a treasure trove of benefits. For starters, it enhances product quality by identifying defects early in the production cycle. It also contributes to more efficient operations by fine-tuning processes based on real data. Furthermore, the use of statistics can lead to cost savings by minimizing waste and maximizing resource allocation.
In short, the significance of statistics in manufacturing cannot be overstated. It enables manufacturers to make informed decisions, streamline operations, and ultimately, stay competitive in an ever-evolving market. Embracing statistical analysis is no longer an option; it’s a necessity for any manufacturing plant aiming for success.
For those looking for a comprehensive overview of statistical tools, consider checking out this AP Statistics formula sheet which covers essential concepts and formulas.
And if you’re eager to dive deeper into the world of statistics, grab a copy of Control Charts for Quality Control. It’s the perfect tool to help you monitor your processes like a hawk!
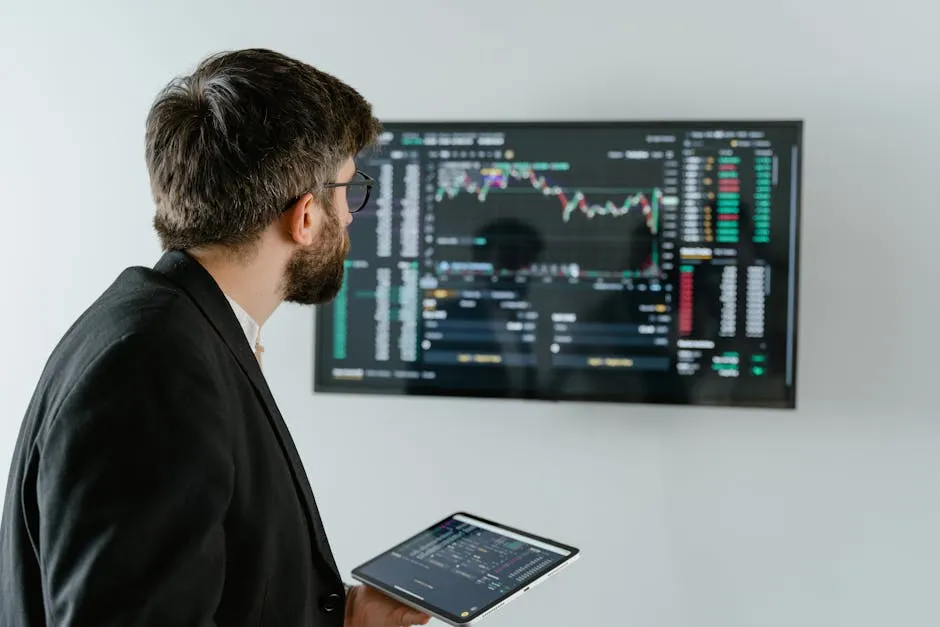
Key Applications of Statistics in Manufacturing
1. Statistical Process Control (SPC)
Definition and Purpose
Statistical Process Control (SPC) is a method that uses statistical techniques to monitor and control manufacturing processes. By applying SPC, manufacturers can ensure their processes operate at their full potential. The primary goal is to identify variations in processes that may lead to defects. Think of it as putting your production line on a diet—cutting out the “fat” of inefficiency while maintaining the “muscle” of quality.
Tools and Techniques
The backbone of SPC includes several powerful tools. Control charts monitor process behavior over time, showing when a process is in control or out of control. For example, a control chart may track the weight of a product over time, flagging any deviations that could indicate problems.
Process capability analysis is another key technique. It assesses how well a process can produce products that meet specifications. A process that’s capable will produce outputs within set limits consistently.
Then there’s Six Sigma—a data-driven approach aiming for near perfection in process performance. It involves identifying and removing causes of defects, thus enhancing quality. Simply put, Six Sigma is like having a superpower for manufacturers; it helps them slash defects and increase customer satisfaction. For a deeper understanding, consider reading Six Sigma: The Breakthrough Management Strategy.
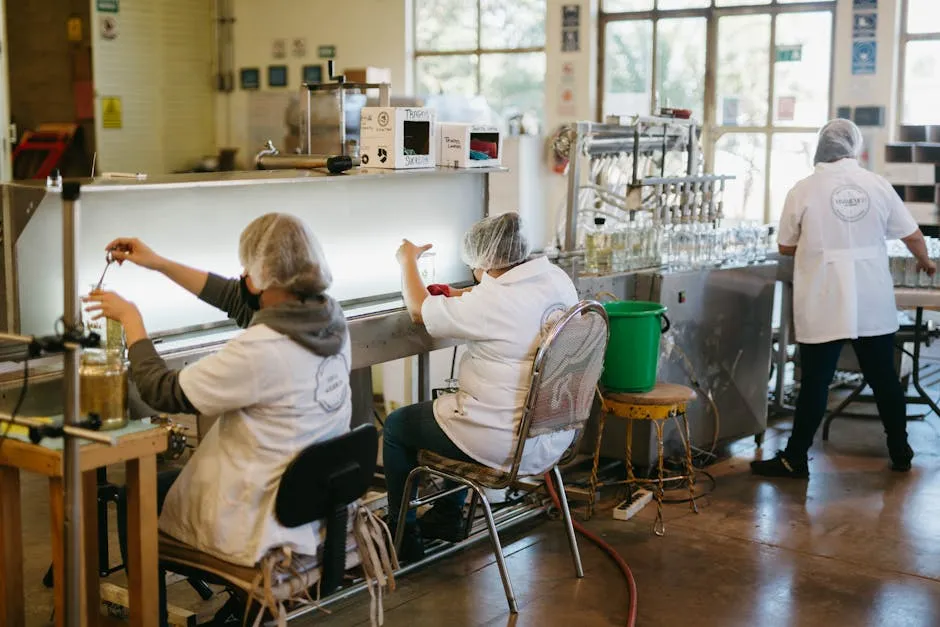
Example
Consider a car parts manufacturer that implemented SPC techniques. By using control charts, they could monitor the thickness of brake pads during production. When they noticed deviations from acceptable limits, they quickly adjusted their machinery. As a result, the company reduced defects by 30% and improved overall product quality. That’s the power of SPC in action!
2. Quality Improvement and Defect Reduction
Statistical Quality Control (SQC)
Statistical Quality Control (SQC) encompasses a variety of statistical methods used to monitor and control quality during manufacturing. By employing SQC, manufacturers can detect defects early in the production process, preventing costly rework or recalls. It’s like having a safety net that catches errors before they fall through the cracks. If you’re interested in mastering SQC, check out Statistical Quality Control: A Modern Approach.
Root Cause Analysis
To address defects effectively, manufacturers must understand their origin. Techniques like Pareto charts and fishbone diagrams are employed to visualize and analyze problems. A Pareto chart helps identify the most significant factors contributing to defects, while a fishbone diagram (or Ishikawa diagram) outlines potential causes of a problem. This systematic approach allows teams to tackle the “big fish” first.
Example
Take a consumer electronics company that noticed a spike in defective products. By deploying SQC methods, they discovered that 70% of defects originated from faulty soldering in one section of the assembly line. Using a fishbone diagram, they identified training gaps as a root cause. They revamped their training program, resulting in a dramatic 50% reduction in defects. Quality improvement isn’t just a goal; it’s achievable through clever analysis!
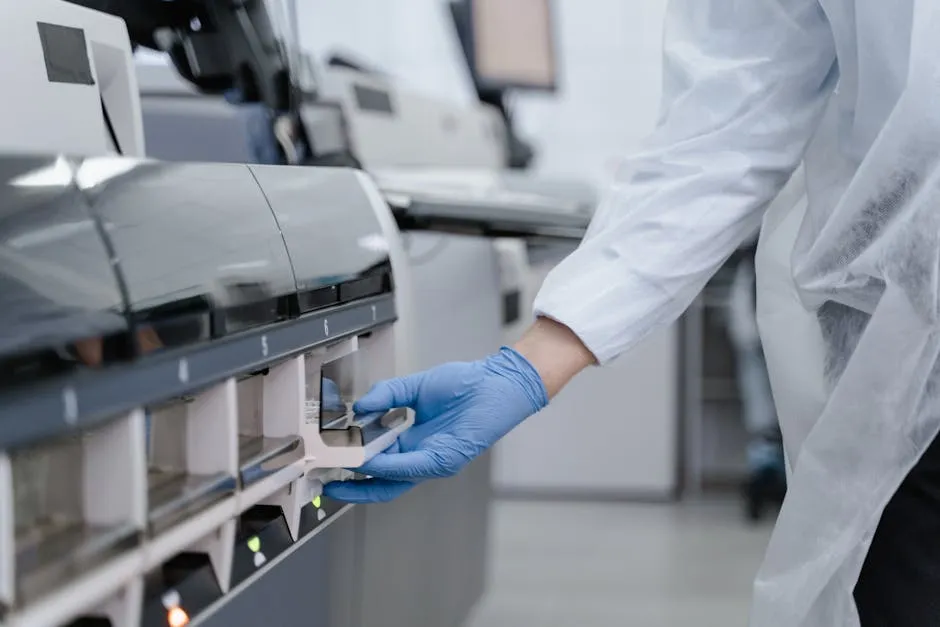
3. Demand Forecasting
Importance of Accurate Forecasting
Accurate demand forecasting is crucial for maintaining efficiency in manufacturing. It allows manufacturers to plan effectively, ensuring they produce just the right amount to meet customer needs. Too much inventory ties up capital, while too little leads to missed opportunities. It’s a delicate balancing act that can make or break a company’s bottom line.
Statistical Methods Used
Manufacturers often turn to statistical methods like regression analysis and time series forecasting for insights. Regression analysis helps identify relationships between variables, such as how past sales data can predict future demand. Time series forecasting, on the other hand, examines historical data to identify patterns over time, allowing manufacturers to plan for seasonal fluctuations. If you’re seeking to enhance your forecasting skills, grab Time Series Analysis: Forecasting and Control.
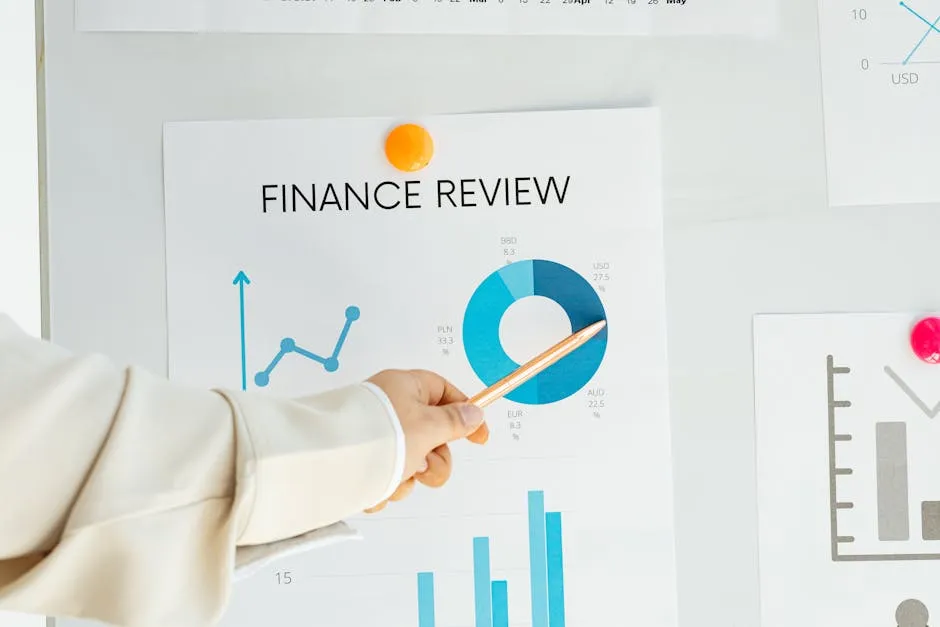
Example
Consider an apparel manufacturer that struggled with inventory management. They implemented regression analysis and time series forecasting to analyze past sales data. By accurately predicting demand for seasonal clothing, they optimized their production schedule, reducing excess inventory by 25%. This data-driven approach not only improved cash flow but also enhanced customer satisfaction by ensuring popular items were always in stock.
4. Production Optimization
Data-Driven Decision Making
In manufacturing, every second counts. Enter statistical analysis—a game changer for production planning and scheduling. By using data-driven insights, manufacturers can fine-tune their processes and boost overall efficiency. Think of it as having a GPS for your production line. Instead of guessing where to go, you get real-time traffic updates and the fastest routes to your destination.
When manufacturers analyze data, they can identify trends and patterns that inform decisions. For instance, if data shows a spike in demand for a specific product, manufacturers can adjust their production schedules accordingly. This proactive approach minimizes downtime and ensures that resources are allocated effectively.
Techniques Used
Two powerful techniques stand out in production optimization: Design of Experiments (DOE) and simulation modeling. If you’re keen on mastering these techniques, you might want to check out Design of Experiments: How to Plan, Analyze, and Present.

Design of Experiments (DOE) helps manufacturers systematically test changes in their processes. By experimenting with different variables—like temperature, pressure, or machine speed—manufacturers can pinpoint the optimal settings that yield the best results. Imagine a chef fine-tuning a recipe until it’s just right. DOE allows manufacturers to achieve similar precision in their production processes.
Simulation modeling, on the other hand, creates a virtual replica of a manufacturing process. This allows companies to run “what-if” scenarios without interrupting actual production. Want to know the impact of adding a new machine? Run a simulation! It’s like playing a video game, where you can experiment with different strategies before committing to one.
Example
Let’s look at a real-world example. A leading automobile manufacturer faced challenges in meeting production targets due to unexpected delays. They decided to implement statistical analysis, focusing on DOE and simulation modeling.
By applying DOE, they tested various production line configurations, revealing that a specific arrangement reduced idle times significantly. Meanwhile, simulation modeling allowed them to forecast the effects of incorporating a new assembly robot. The results were eye-opening! After making the changes, the company reported a 20% increase in throughput within just three months.
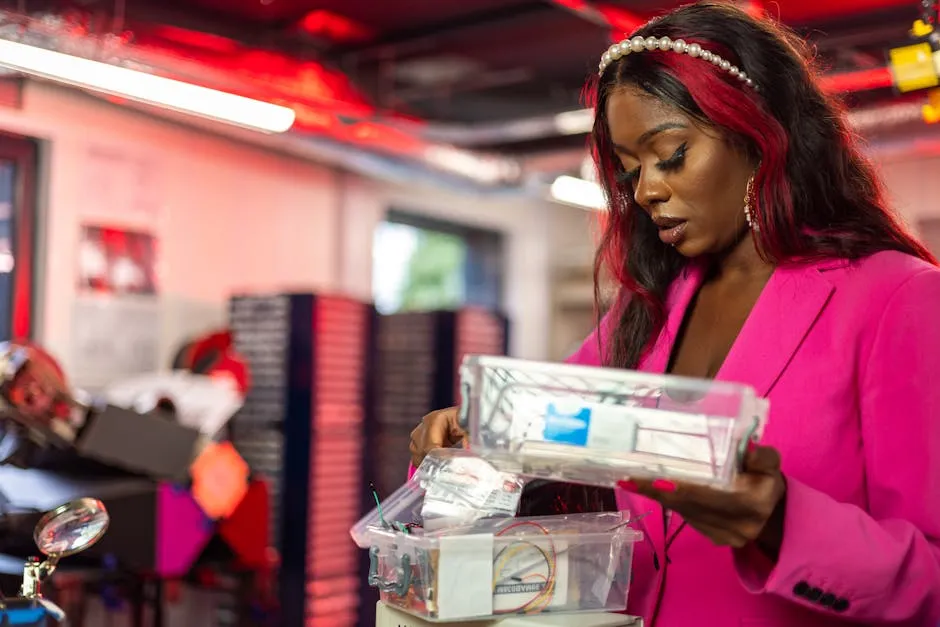
This case illustrates how embracing statistical techniques can lead to tangible improvements. In manufacturing, optimizing production isn’t just a luxury; it’s a necessity for staying competitive. With data guiding the way, manufacturers can confidently navigate the complexities of production optimization.
5. Predictive Maintenance
Overview
Predictive maintenance is like having a crystal ball for equipment management. It uses data and statistical techniques to predict when a machine is likely to fail. This proactive approach can save manufacturers time and money while minimizing downtime.
The benefits are substantial. Predictive maintenance reduces the chances of unexpected breakdowns, allowing for scheduled repairs before issues escalate. Imagine avoiding a last-minute production halt because a machine has failed. Instead, maintenance teams can plan repairs during off-hours, keeping operations running smoothly. If you want to know more about predictive maintenance, check out Predictive Maintenance: A Practical Guide.
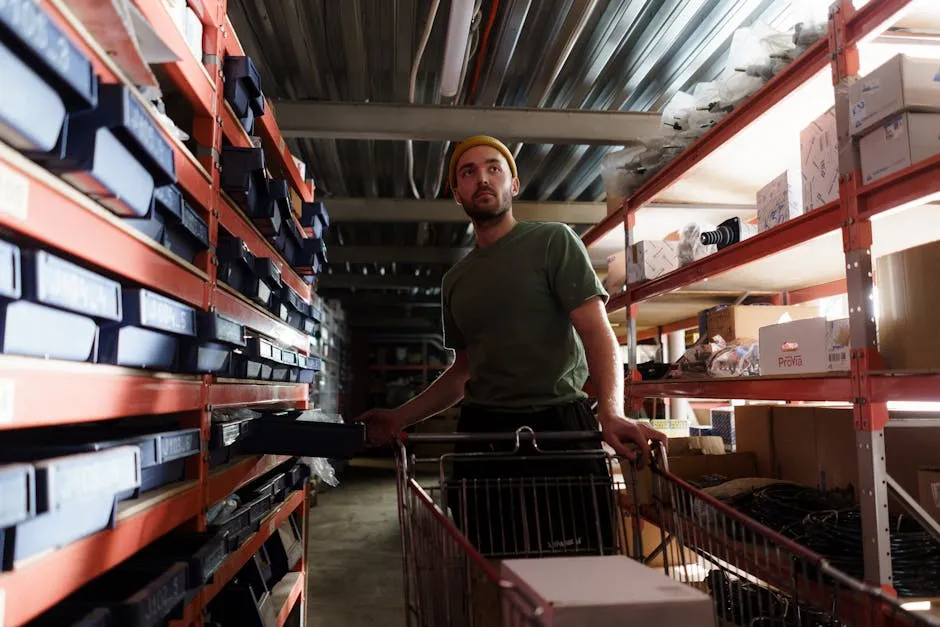
Statistical Techniques
At the heart of predictive maintenance are statistical models that analyze historical data to forecast equipment failures. Techniques such as regression analysis and time series forecasting help identify patterns. By evaluating metrics like temperature, vibration, and usage hours, manufacturers can spot anomalies that suggest impending failure.
For instance, if a machine’s vibration levels increase beyond normal thresholds, predictive models can alert operators to investigate further. This early warning system not only enhances reliability but also improves overall efficiency.
Example
Take the example of a large manufacturing plant that produces consumer goods. By implementing predictive analytics, they were able to reduce their equipment downtime by 30%. They analyzed historical maintenance records and machine data to create a predictive model that highlighted potential failures in advance.
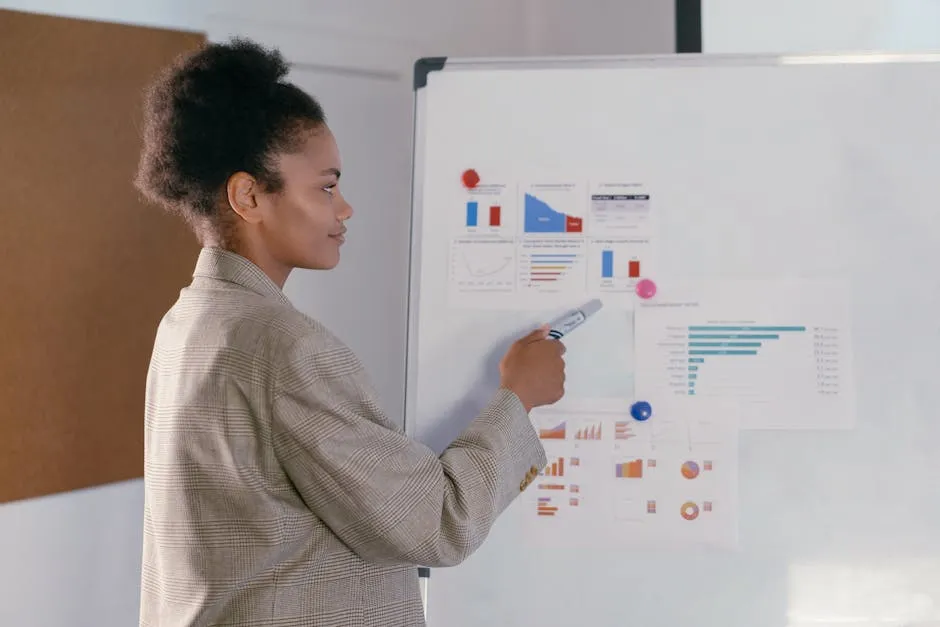
As a result, maintenance teams could address issues before they caused significant disruptions. This proactive approach not only cut repair costs but also boosted productivity, as the plant avoided costly production halts.
In conclusion, predictive maintenance transforms the way manufacturers approach equipment management. With statistical analysis as a guiding light, businesses can enhance reliability, reduce costs, and ensure smooth operations.
6. Inventory Management
Challenges in Inventory Management
Inventory management can feel like walking a tightrope. Manufacturers face numerous challenges, from stockouts to overstocking, which can lead to lost sales or unnecessary carrying costs. Striking the right balance is crucial for maintaining profitability.
Common issues include inaccurate demand forecasting, lack of visibility into inventory levels, and inefficient replenishment processes. These challenges can result in excess inventory or insufficient stock to meet customer demands. If you’re looking to optimize your inventory management, consider Inventory Management: Principles, Concepts, and Techniques.
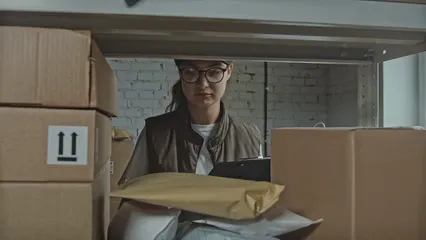
Statistical Tools
Statistical methods offer relief in the form of inventory optimization techniques. Techniques such as Economic Order Quantity (EOQ) and Just-In-Time (JIT) inventory management help manufacturers determine the ideal amount of inventory to keep on hand.
EOQ calculates the most cost-effective quantity to order by considering demand, ordering costs, and holding costs. On the other hand, JIT focuses on minimizing inventory levels by receiving goods only as needed. This approach reduces waste and ensures that capital is not tied up in excess stock.
Example
Consider a food manufacturer that struggled with inventory turnover rates. By implementing statistical analysis and inventory optimization techniques, they were able to improve their processes significantly.
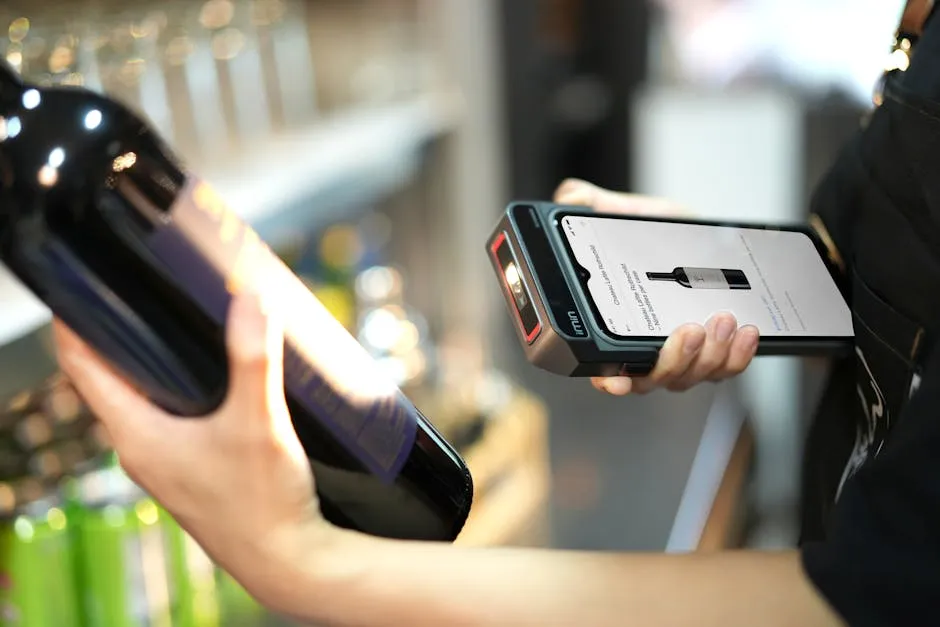
Using EOQ, they determined the optimal order quantities, resulting in a 40% reduction in holding costs. Additionally, by adopting JIT principles, they minimized waste, ensuring that products remained fresh and reducing spoilage.
Through data analysis and statistical methods, the company enhanced its inventory management, ultimately increasing turnover rates and boosting profitability. By leveraging statistics, manufacturers can navigate the complexities of inventory management and achieve operational excellence.
7. Employee Performance and Productivity Analysis
Importance of Human Factors
In manufacturing, employees are the backbone of productivity. Assessing employee performance through statistics is like having a backstage pass to the concert of efficiency. Statistics help identify who’s hitting all the right notes and who might need a little extra practice. By measuring productivity levels, managers can pinpoint strengths and weaknesses among their teams.
Imagine a factory where workers are producing widgets at lightning speed. Thanks to statistical analysis, supervisors can track the output of each employee. This data reveals who consistently meets or exceeds targets and who might be struggling. Such insights are invaluable for fostering a work environment that encourages growth and improvement.
Methods
Employing workforce analytics and performance metrics can transform how manufacturers manage their teams. Workforce analytics involve collecting and analyzing data on employee performance, attendance, and even engagement levels. This data can highlight trends, such as which shifts have the most productive employees or if certain teams are consistently underperforming.
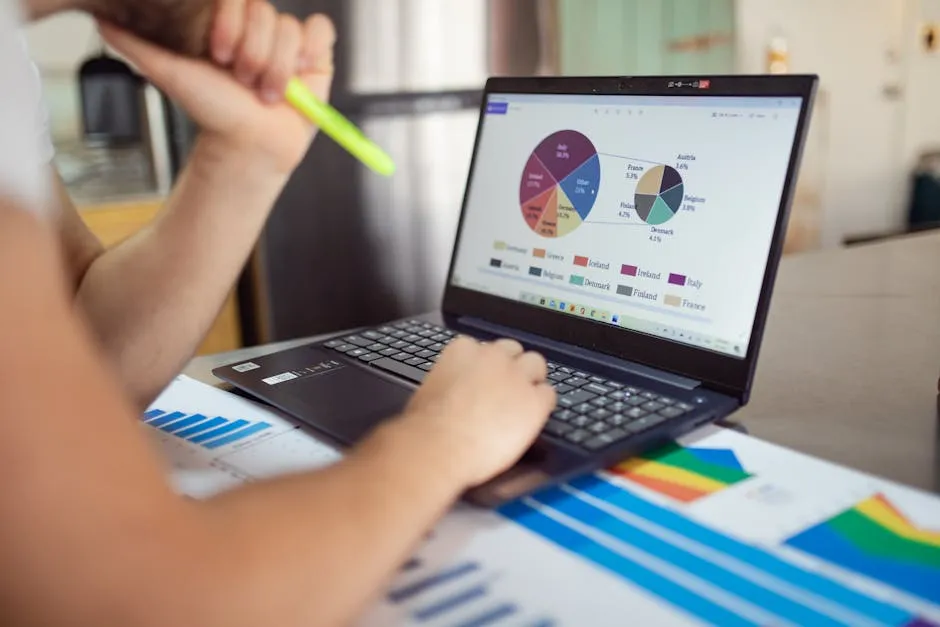
Performance metrics, on the other hand, are the key performance indicators (KPIs) that help measure employee output. Metrics like the number of units produced, defect rates, and adherence to safety protocols provide a quantifiable way to evaluate performance. For those interested in enhancing their performance evaluation process, consider using Employee Performance Evaluation Software.
One popular approach is using 360-degree feedback, where input is gathered from various sources—peers, supervisors, and even subordinates. This method offers a well-rounded view of employee contributions. By combining these analytics with performance metrics, manufacturers can develop training programs tailored to individual needs.
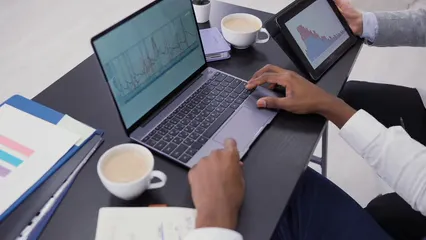
Example
Let’s look at the case of a manufacturing plant that produces automotive parts. This plant implemented a statistical analysis program to track employee performance. By collecting data on production rates and defect levels, they discovered that a specific team consistently produced 20% more parts than others.
Upon further investigation, they found that this team had adopted a new tool that improved their workflow. Instead of just celebrating their success, management decided to conduct training sessions for other teams based on this team’s techniques. Within a few months, overall productivity increased across the board, leading to significant cost savings and a boost in employee morale.
In another instance, a clothing manufacturer noticed a high defect rate in a particular sewing department. By analyzing statistical data, they found that the high turnover rate among employees led to insufficient training. Management addressed this by implementing a mentorship program, resulting in a 30% reduction in defects.
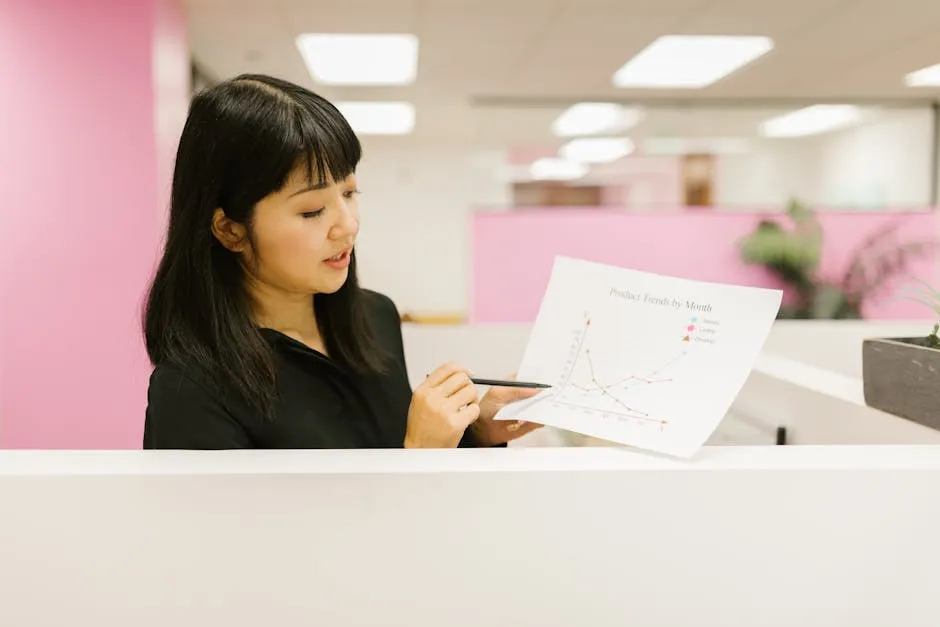
These examples illustrate how statistics can revolutionize employee performance analysis. By leveraging data, manufacturers can make informed decisions that not only enhance productivity but also create a more engaged workforce.
Encouraging a culture of continuous improvement through statistical analysis can lead to higher job satisfaction and retention rates. In the end, it’s not just about numbers; it’s about valuing human potential in the manufacturing landscape.
FAQs
What statistical tools are commonly used in manufacturing?
Manufacturing relies on several powerful statistical tools to analyze data and improve processes. Here are three popular options: Minitab: This software specializes in statistical analysis. It helps users create control charts, conduct hypothesis testing, and perform regression analysis. Minitab’s user-friendly interface makes it a favorite among manufacturers for quality improvement. MATLAB: Known for its numerical computing environment, MATLAB is used for data analysis, algorithm development, and visualization. Manufacturers utilize MATLAB to model complex systems and analyze large datasets, enabling better decision-making in production. R: As a free programming language, R is a fantastic option for statistical computing and graphics. It boasts a wide array of packages for various analyses, including time series and regression. R is popular among data scientists in manufacturing due to its flexibility and extensive community support.
How can small manufacturers implement statistical methods?
Small manufacturers can implement statistical methods by starting with simple, cost-effective strategies: 1. Training: Invest in basic training for staff to understand key statistical concepts. Online courses or workshops can be beneficial. 2. Data Collection: Use existing data sources, like production logs, to track performance metrics. Start small by focusing on a few critical measurements. 3. Software Tools: Utilize free or low-cost statistical software like R or Excel for data analysis. These tools can help visualize results and identify patterns. 4. Collaboration: Partner with local universities or organizations that have expertise in statistics. Collaborative projects can provide valuable insights without a significant investment. 5. Continuous Improvement: Adopt a culture of continuous improvement. Encourage employees to suggest data-driven changes based on statistical analysis.
What are the challenges of using statistics in manufacturing?
Manufacturers often face several challenges when implementing statistics in their operations: 1. Data Quality: Inaccurate or incomplete data can lead to misleading analyses. Ensuring data integrity is crucial for reliable results. 2. Staff Training: Many employees may lack statistical knowledge. Training is necessary but can be time-consuming and costly. 3. Resistance to Change: Some employees may be reluctant to adopt new methods. Overcoming this resistance requires effective communication and demonstrating the benefits of statistical approaches. 4. Integration: Incorporating statistical methods into existing processes can be complex. Manufacturers must ensure that new methods align with current workflows. 5. Resource Limitations: Smaller manufacturers may lack the resources for advanced statistical tools or expertise, making it difficult to leverage data effectively.
How does Industry 4.0 impact the use of statistics in manufacturing?
Industry 4.0 has transformed the manufacturing landscape by integrating IoT devices and big data analytics. This shift enhances the use of statistics in several ways: 1. Real-Time Data: IoT devices provide continuous data streams, allowing manufacturers to analyze processes in real-time. This immediate feedback leads to quicker decision-making. 2. Predictive Analytics: With big data analytics, manufacturers can forecast trends and predict equipment failures. This proactive approach minimizes downtime and enhances efficiency. 3. Improved Processes: Advanced statistical methods can identify bottlenecks and inefficiencies, leading to optimized production processes. 4. Enhanced Quality Control: Industry 4.0 technologies enable better monitoring of quality metrics, helping manufacturers maintain high standards and reduce defects. 5. Data-Driven Culture: The emphasis on data in Industry 4.0 encourages a culture of data-driven decision-making, promoting continuous improvement across the organization.
Can statistics help in sustainability efforts in manufacturing?
Absolutely! Statistics play a crucial role in promoting sustainability in manufacturing by enabling data-driven decisions. Here’s how: 1. Resource Optimization: By analyzing data on resource usage, manufacturers can identify areas to reduce waste and lower energy consumption. 2. Sustainability Metrics: Statistical methods can track key sustainability indicators, such as carbon emissions and material usage, allowing manufacturers to set and meet sustainability goals. 3. Process Improvement: Statistical analysis helps find inefficiencies in production processes, leading to reduced waste and improved environmental performance. 4. Lifecycle Assessment: Manufacturers can use statistics to evaluate the environmental impact of their products throughout their lifecycle, informing better design and material choices. 5. Regulatory Compliance: Data analysis aids in monitoring compliance with environmental regulations, ensuring that companies adhere to legal standards and enhance their reputation.
Please let us know what you think about our content by leaving a comment down below!
Thank you for reading till here 🙂
All images from Pexels