Introduction
Statistical Process Control (SPC) is more than just a fancy term to throw around in quality meetings. It’s a method that uses statistical techniques to monitor and control processes. Think of it as the superhero of quality management—flying in to save the day by ensuring that your processes are efficient and produce high-quality products. Whether in manufacturing, healthcare, or even finance, SPC helps businesses maintain their reputation while keeping costs in check.
Now, why should you care about having processes in statistical control? Well, imagine a world where every product you buy meets your expectations. No surprises, no disappointments. That’s the magic of SPC! It ensures consistency and quality, making it easier for companies to deliver what they promise. In a competitive market, where every little detail matters, having a process that is in control can mean the difference between success and failure.
This article aims to demystify SPC for you. We’ll cover what SPC is, how to determine if a process is in control, and practical applications you can take back to your organization. So, buckle up! We’re about to embark on a statistical adventure that promises to be both enlightening and engaging. Let’s ensure your processes are not just running but are in tip-top shape!
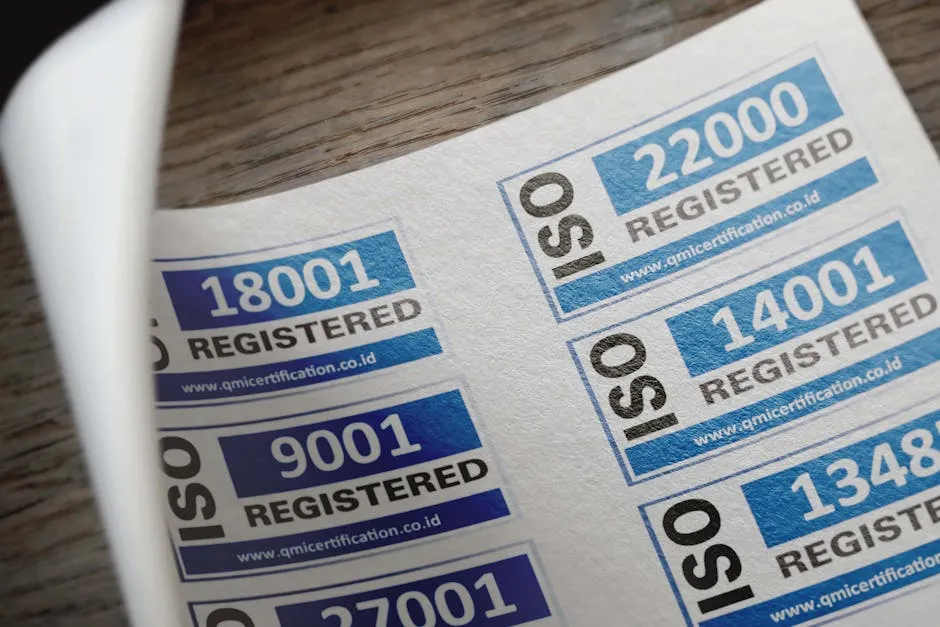
Understanding Statistical Process Control (SPC)
What is SPC?
Statistical Process Control (SPC) is a robust method for monitoring quality during production. By applying statistical methods, businesses can track and control quality throughout their processes. The concept was first introduced by Walter A. Shewhart in the 1920s when he developed the control chart. This revolutionary tool allowed manufacturers to visualize process data over time.
Fast forward a few decades, and SPC gained popularity thanks to W. Edwards Deming, who championed these techniques during his training programs in post-war Japan. Today, SPC is essential in modern industries, from automotive to healthcare, where maintaining quality is non-negotiable.
If you’re looking to dive deeper into SPC, a great resource is the Quality Control Handbook. This book offers a comprehensive look at quality control principles and practices that can take your understanding of SPC to the next level.

Key Components of SPC
SPC isn’t just a one-trick pony; it’s a comprehensive toolbox. The main tools include control charts, which help visualize process performance over time, and process capability analysis, which assesses how well a process can produce items within specifications. Variation analysis is another critical component that distinguishes between common causes (inherent to the process) and special causes (external factors that can disrupt normal operations).
Data is the lifeblood of SPC, and it typically falls into two categories: variable data, which involves measurable quantities (like weight or temperature), and attribute data, which deals with discrete outcomes (like pass/fail). Each type of data requires specific tools for effective analysis.
In summary, SPC is a powerful framework that combines statistical methods with real-world applications. It helps companies maintain high standards while minimizing waste and maximizing efficiency. So, whether you’re in a factory or a service center, understanding SPC is vital for anyone serious about quality.
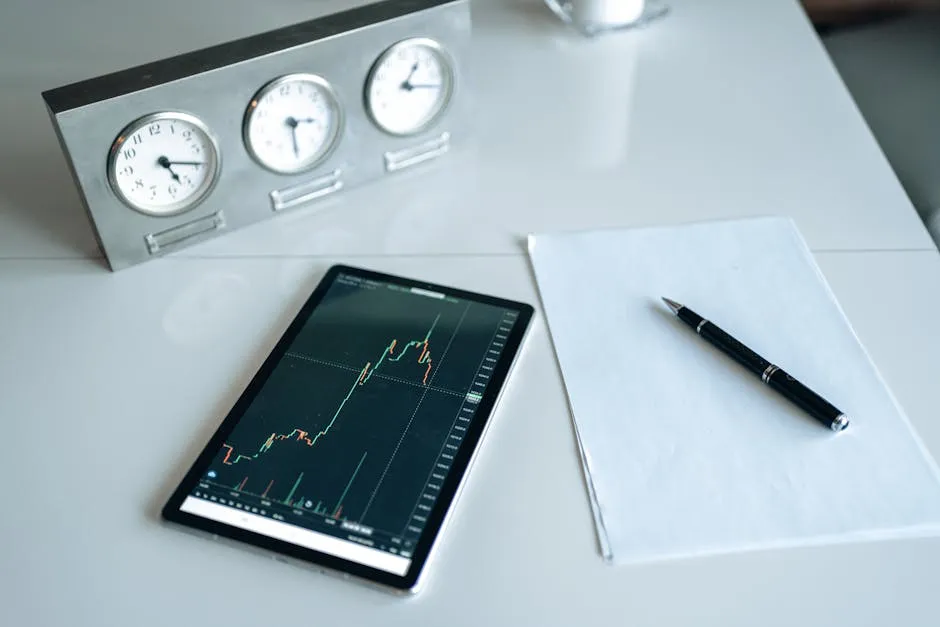
The Importance of Being in Statistical Control
Benefits of SPC
First off, let’s talk waste reduction. Imagine a world where every component produced is spot on, and there’s hardly any need for rework. SPC helps achieve this by identifying and eliminating variations before they lead to defects. This proactive approach means less scrap and fewer resources wasted—like finding a secret stash of cash you didn’t know existed!
Next up, improved product quality and consistency. Nobody likes surprises when they open a package. With SPC, companies can ensure that the products meet specifications every time. It’s like having a reliable friend who always shows up on time—customers come to trust your brand because they know what to expect.
Operational efficiency gets a boost too. By focusing on statistical control, organizations can streamline processes, reduce downtime, and ultimately save money. It’s like switching from a clunky old bicycle to a sleek road bike; the difference in performance is night and day.
If you’re looking for a handy guide to help you implement these principles, check out the The Lean Six Sigma Pocket Toolbook. It’s packed with tools and techniques to help streamline your processes and improve quality.
But wait, there’s more! SPC also enhances the ability to identify and resolve issues proactively. Think of it as a crystal ball for your processes—allowing you to foresee potential hiccups before they escalate into full-blown disasters. With timely insights, teams can make necessary adjustments, keeping operations smooth and uninterrupted.

Common and Special Causes of Variation
Now, let’s dive into the types of variations that can impact your processes. Understanding these is crucial for maintaining statistical control.
Common cause variation refers to the natural fluctuations inherent in any process. These variations are stable and predictable, much like the changing seasons. They can arise from factors such as machine wear, material inconsistencies, or even shifts in environmental conditions. While they are expected, it’s essential to monitor them closely.
On the flip side, we have special cause variation. This type is the troublemaker of the group! Special causes are unexpected and can lead to significant disruptions. Think of them as the rogue wave that suddenly appears in calm waters. These variations may stem from equipment malfunctions, human errors, or sudden shifts in the production process. Identifying these causes quickly is vital to restoring control and ensuring processes remain stable.
In summary, the benefits of being in statistical control are numerous. From reducing waste and improving quality to enhancing efficiency and identifying issues, SPC is your go-to strategy. Understanding the nuances of common and special cause variations empowers organizations to maintain control and achieve consistent excellence in their outputs. So, let’s keep those processes in check and sail smoothly toward success!

Common Challenges and Solutions
Implementing Statistical Process Control (SPC) isn’t all rainbows and butterflies. Organizations often encounter various bumps on the road. Let’s explore some common hurdles and how to leap over them like a pro!
1. Resistance to Change
Humans are creatures of habit. When faced with new methods, such as SPC, many employees may resist. They might cling to old ways, fearing the unknown. To combat this, communication is key. Explain the benefits of SPC clearly and involve team members in the transition process. Make them feel part of the journey, not just passengers. Celebrating small wins can also boost morale and buy-in.
2. Data Collection Issues
Gathering accurate data is like herding cats—challenging but essential. Inconsistent or poorly collected data can lead to misleading results. To remedy this, establish clear protocols for data collection. Train staff thoroughly on these methods. Using technology, like automated systems, can also help ensure data accuracy and consistency.
3. Training Requirements
SPC techniques can seem daunting, especially for those unfamiliar with statistics. Fear not! Offering comprehensive training is the answer. Whether through workshops or online courses, equip your team with the necessary knowledge. Remember, a well-trained team is a confident team. They’ll be more likely to embrace SPC and contribute positively to the process.
4. Overcomplicating the Process
Sometimes, in an effort to do things “right,” organizations complicate SPC implementation. Keep it simple! Focus on the basics first. Start with a few key processes before scaling up. This approach allows for manageable adjustments and gradual learning. It’s like training for a marathon—start with a few laps, then work your way up!
5. Integration with Existing Systems
Integrating SPC with current processes can be tricky. Different teams may use various methods, leading to confusion. To tackle this, ensure that SPC fits organically into your existing framework. Foster collaboration between departments to create a unified approach. A smooth integration, like a well-choreographed dance, can lead to spectacular results!
In summary, while implementing SPC can present challenges, they’re not insurmountable. With effective communication, thorough training, and a focus on simplicity, organizations can overcome these obstacles and reap the rewards of a controlled, optimized process.
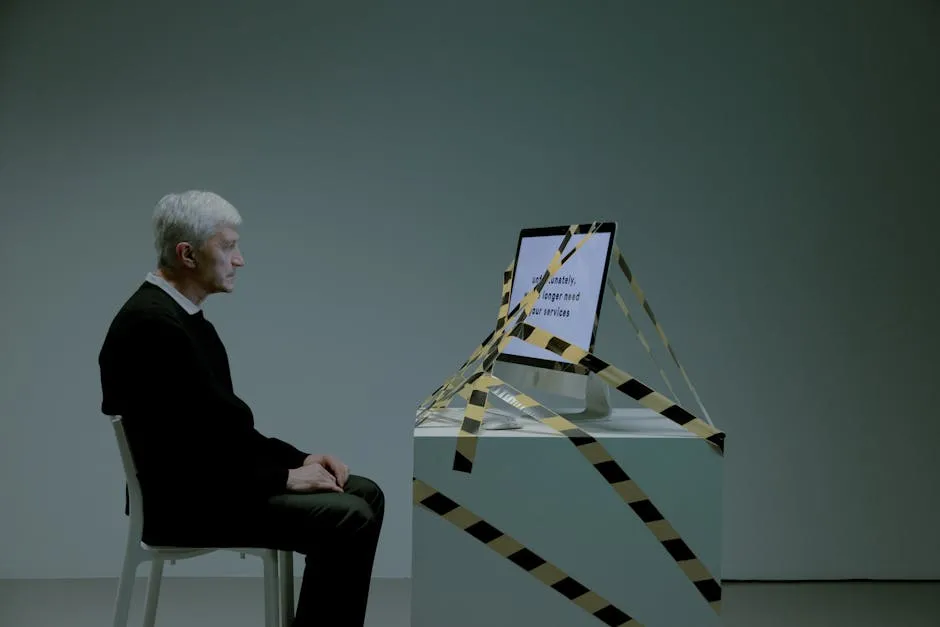
Analyzing SPC Data
Interpreting Control Charts
Control charts are the backbone of Statistical Process Control (SPC). They visualize how a process performs over time. Understanding how to read these charts is crucial for effective analysis.
Reading Control Charts
At first glance, control charts may seem like a jumble of lines and points. Fear not! Let’s break it down. A control chart typically features a center line representing the process average. There are also upper and lower control limits, usually set at three standard deviations from the mean. If most points are huddled around the center line, you’re in good shape; the process is in control!
Points Outside Control Limits
What happens when points stray outside these control limits? Uh-oh! This indicates a special cause variation, which demands immediate attention. Think of it as a red flag waving at a soccer game—something’s off, and it needs investigating. Identifying these points allows teams to pinpoint problems before they escalate.
Patterns Indicating Special Causes
But it’s not just about the outliers! Patterns on the chart can signal special causes too. If you see a trend of increasing or decreasing points, it suggests something might be amiss. For instance, seven points in a row moving upward could signal a shift in the process—time to dig deeper!

Process Capability Analysis
Now that we know how to interpret control charts, let’s dive into process capability analysis. This is all about understanding how well a process can meet specifications.
Defining Process Capability
Process capability refers to the ability of a process to produce output that meets defined specifications consistently. It’s like a quality report card, giving insight into whether your process can deliver the goods. A capable process is one that produces outputs within specified limits, ensuring customer satisfaction.
Calculating Capability Indices (Cp, Cpk)
To quantify process capability, we use capability indices like Cp and Cpk. Here’s how it works:
– Cp measures potential capability by comparing the spread of the process against the specification limits. A Cp of 1.0 indicates that the process can meet specifications, but there’s room for improvement.
– Cpk goes a step further by considering how centered the process is within those limits. A Cpk of 1.0 means the process is just meeting specifications, while a Cpk greater than 1.33 is often considered adequate for most industries.
In conclusion, understanding control charts and process capability is essential for effective SPC. By mastering these concepts, organizations can ensure their processes are in control and capable of delivering quality results. A well-tuned process is not just a dream—it’s an achievable reality!

Case Studies: SPC in Action
Statistical Process Control (SPC) has transformed numerous organizations, turning their quality management practices from reactive to proactive. Let’s take a peek at some real-world examples to see how SPC has worked wonders.
1. Toyota Motor Corporation
Toyota is renowned for its commitment to quality. The company adopted SPC techniques as part of its Toyota Production System (TPS). By utilizing control charts to monitor production processes, Toyota identified variations early. This approach led to a significant reduction in defects and improved product reliability. In the late 1990s, Toyota reported a defect rate that was 50% lower than its competitors. The result? A stellar reputation that propelled them to the top of the automotive industry.
For those interested in the principles behind Toyota’s success, consider reading The Toyota Way: 14 Management Principles from the World’s Greatest Manufacturer. This book dives deep into the philosophies that drive Toyota’s success.
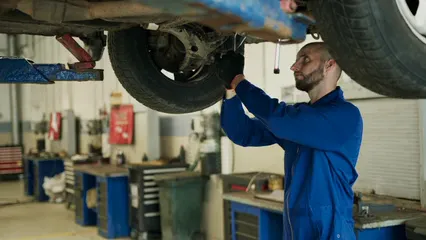
2. Boeing
Boeing faced immense pressure to enhance quality while reducing costs in its airplane manufacturing. By implementing SPC, they monitored key processes throughout production. Control charts helped Boeing minimize the variability in assembly operations, leading to a 20% reduction in assembly time. This not only cut costs but also improved the overall quality of their aircraft. Today, Boeing continues to utilize SPC as a cornerstone of its quality control strategy.
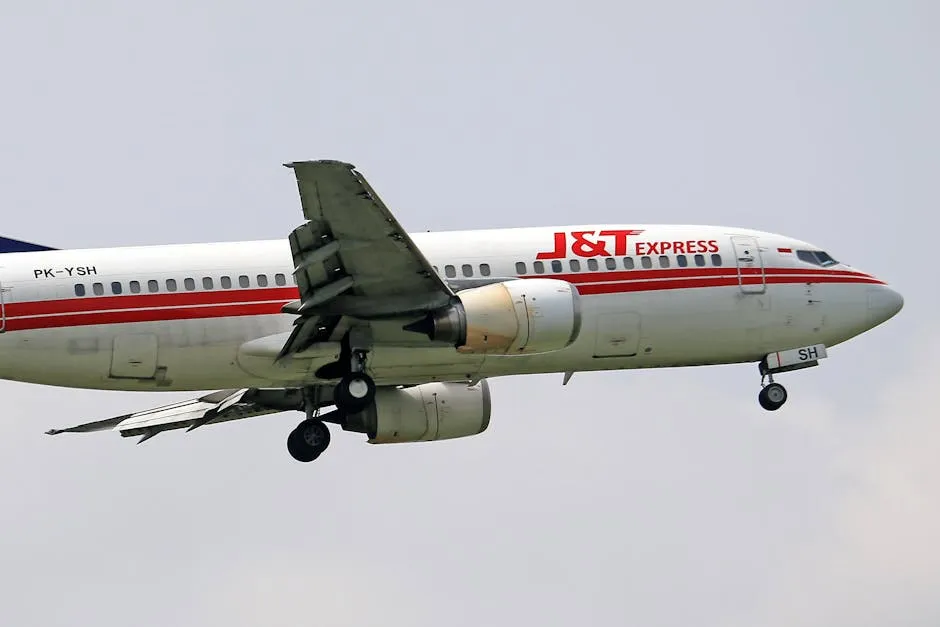
3. The NHS (National Health Service)
The NHS implemented SPC tools to improve patient care and operational efficiency. By employing SPC charts, they tracked patient wait times and treatment outcomes. This data-driven approach enabled the NHS to identify patterns and implement changes that reduced waiting times by up to 30% in certain departments. The use of SPC not only enhanced patient satisfaction but also allowed staff to focus on delivering quality care.
For healthcare professionals interested in quality improvement, the book Quality Improvement: A Guide for the Health Care Professional is a must-read. It offers practical strategies for enhancing healthcare quality.
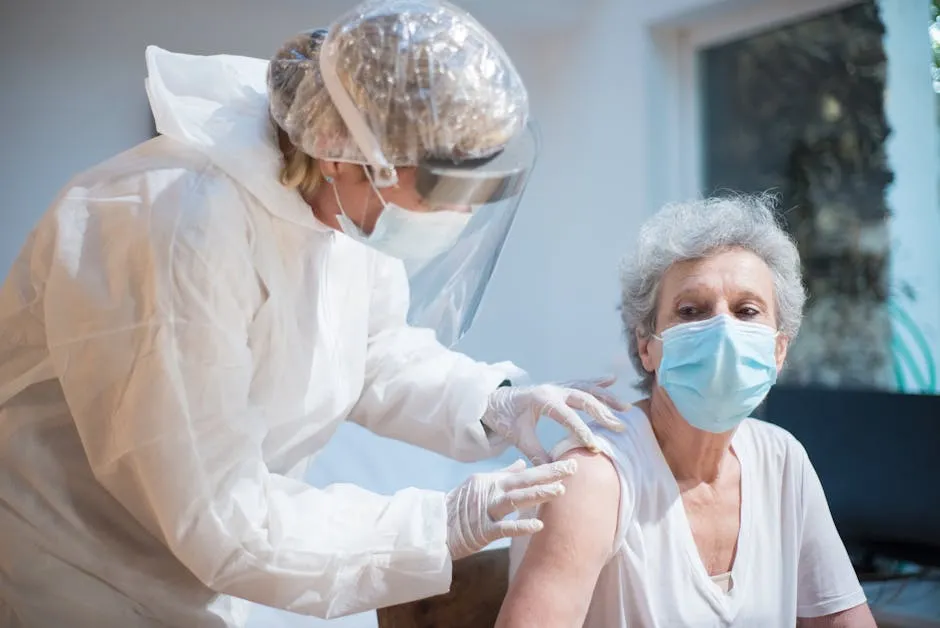
4. 3M
3M is famous for its innovative products, but sustaining quality while fostering creativity can be challenging. Through SPC, 3M monitored numerous production processes simultaneously. By analyzing data from control charts, the company significantly reduced waste and rework costs. In one facility, 3M achieved a 40% reduction in scrap material, translating to substantial cost savings and a greener footprint.
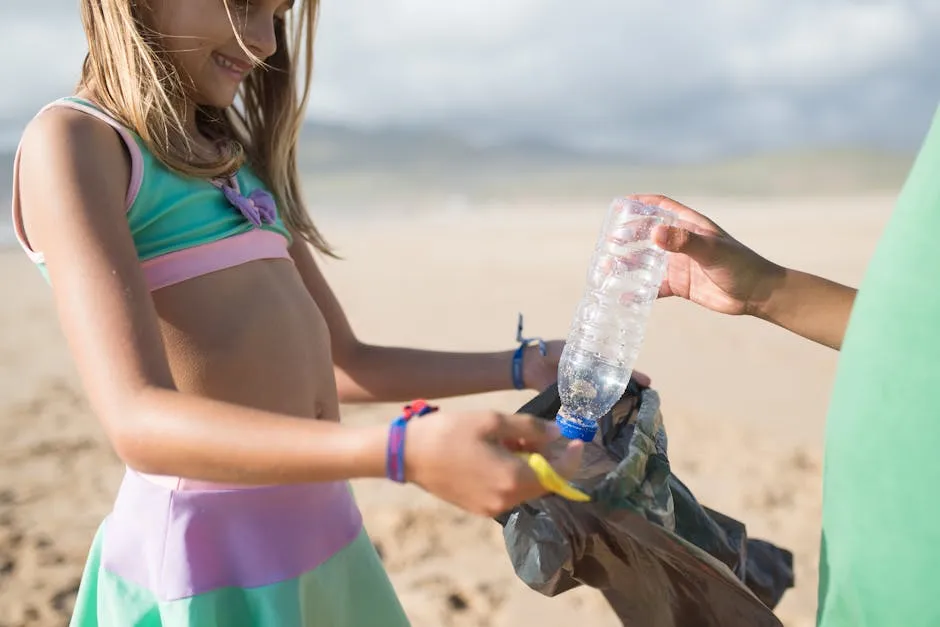
5. Starbucks
Even a coffee giant like Starbucks benefits from SPC. By analyzing customer feedback and operational data, Starbucks uses SPC techniques to maintain consistency across its stores. Control charts help them monitor factors like brewing time and temperature. This ensures every cup of coffee meets their high standards. As a result, Starbucks has seen improved customer satisfaction and loyalty, solidifying its position in the coffee industry.
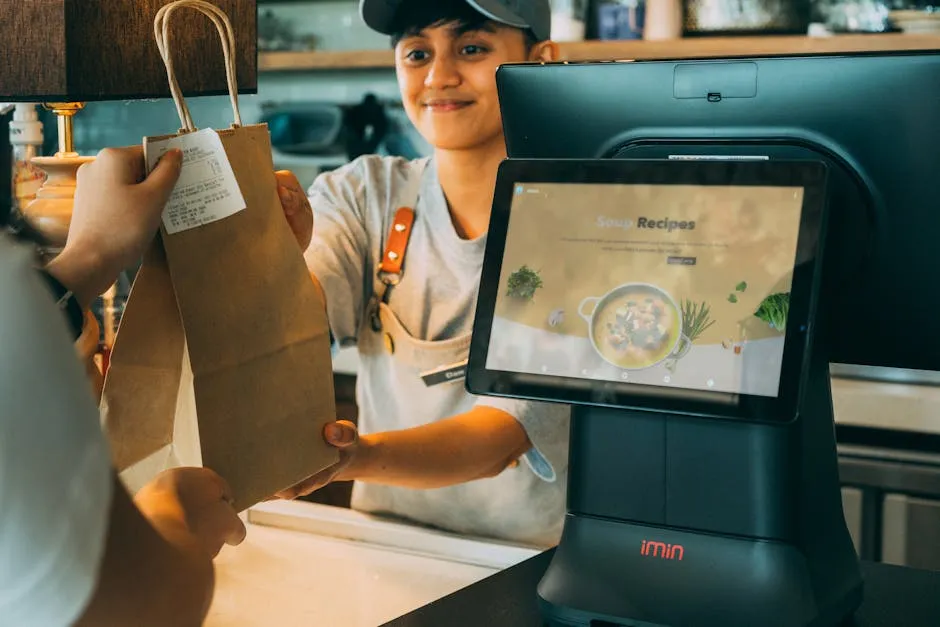
Outcomes Achieved Through SPC Practices
These organizations have not just implemented SPC; they’ve thrived because of it. The outcomes speak volumes:
- Quality Improvement: Each case study highlights significant reductions in defects and enhanced product reliability.
- Cost Reduction: Companies like Boeing and 3M have realized substantial savings through minimized waste.
- Operational Efficiency: The NHS and Toyota showcased how SPC can streamline processes, leading to shorter wait times and faster production cycles.
- Customer Satisfaction: By ensuring consistent quality, Starbucks has maintained a loyal customer base, crucial in today’s competitive market.
In conclusion, the successful implementation of SPC across various industries demonstrates the methodology’s versatility. Organizations that embrace SPC not only foster a culture of quality but also position themselves for long-term success in their respective markets.

Conclusion
Statistical Process Control (SPC) is more than just a set of tools; it’s a philosophy that can elevate organizational performance. Throughout this article, we’ve explored the critical aspects of SPC, including its definition, key components, and implementation strategies. The case studies illustrated real-world success stories, showing how SPC has helped companies like Toyota and Boeing enhance their quality management practices.
The key takeaways are clear: SPC helps organizations maintain quality and efficiency in their processes. It allows businesses to identify variations proactively, minimizing waste and improving overall performance. In an ever-competitive landscape, adopting SPC can be the difference between mediocrity and excellence.
As you reflect on your own organization, consider the potential benefits of implementing SPC. Whether you’re in manufacturing, healthcare, or service industries, SPC can be tailored to fit your needs. By focusing on continuous improvement and data-driven decision-making, you can foster a culture of quality that resonates throughout your organization.
If you want to delve deeper into the concepts of SPC and quality management, check out Statistical Methods for Quality Improvement. It’s an insightful read that provides practical tools and techniques for enhancing quality.
So, are you ready to embrace SPC? Taking that first step could lead to remarkable transformations in your processes and, ultimately, your bottom line. Let’s make quality a habit, not an afterthought!
FAQs
What is the difference between common cause and special cause variation?
Common cause variation refers to the inherent fluctuations present in any process. It’s like the background noise you hear while enjoying your favorite tune—always there and predictable. These variations are stable, stemming from factors like equipment wear and tear or slight changes in material properties. On the other hand, special cause variation is the unexpected guest at your party. These anomalies disrupt the usual flow, often arising from external factors like machine malfunctions or sudden changes in production methods. Unlike common causes, special causes are sporadic and unpredictable. Identifying and addressing these variations is key to maintaining statistical control.
How can I start implementing SPC in my organization?
Ready to roll up your sleeves and dive into Statistical Process Control (SPC)? Start by identifying critical processes that impact quality and efficiency. Next, gather reliable data—this is the bedrock of effective SPC. Once you have your data, choose the right control chart to visualize your process performance. Setting control limits is crucial; these will help you spot when things go awry. Finally, don’t forget to train your team on monitoring and analyzing the data. Remember, the goal is continuous improvement, not just a one-time fix!
What tools are commonly used in SPC?
SPC comes with a toolbox full of handy instruments! Control charts take the lead, allowing organizations to visualize process performance over time. Other vital tools include histograms, which display frequency distributions, and Pareto charts, often used to highlight the most common issues. Cause-and-effect diagrams (Ishikawa or fishbone diagrams) help identify potential sources of problems. Lastly, check sheets and scatter diagrams can assist in data collection and relationship analysis. With these tools in your arsenal, you’ll be well-equipped to tackle variability!
Can SPC be applied outside of manufacturing?
Absolutely! While SPC has strong roots in manufacturing, its applications stretch far beyond factory floors. Industries like healthcare, finance, and even IT operations can harness SPC to improve processes. For instance, hospitals can use SPC to monitor patient wait times or treatment outcomes, ensuring consistent quality in care. Similarly, financial institutions can apply SPC to track transaction processes or loan approvals. By embracing SPC, organizations can enhance efficiency and quality, regardless of the sector they belong to.
How do I know if my process is in statistical control?
Determining if your process is in statistical control is like checking the pulse of your operations. The first step is to plot your data on a control chart. If most of your data points dance around the center line, staying within the control limits, congratulations! Your process is in control. However, if you spot points straying outside these limits or notice non-random patterns, it signals special cause variation. At this point, it’s time to investigate further. Regular monitoring and analysis will help ensure your process remains stable and efficient.
Please let us know what you think about our content by leaving a comment down below!
Thank you for reading till here 🙂
For more insights on statistical process control, check out this discussion on statistical process control anomaly reddit.
All images from Pexels